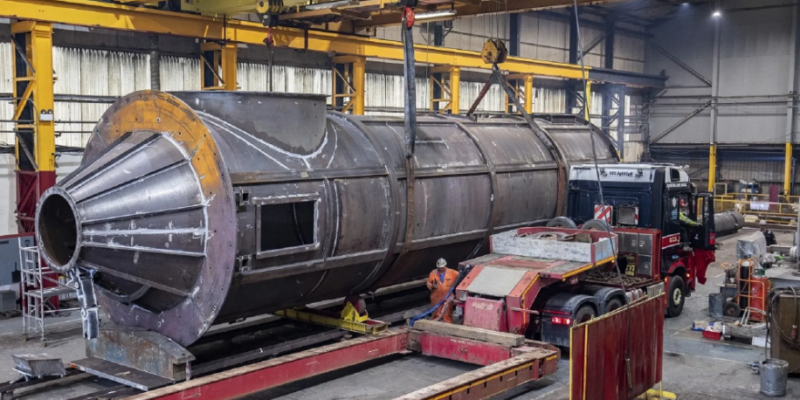
Francis Brown has fabricated the largest single item to emerge from its Teesside workshops during its 120-year history.
The 32-ton vertical firing chamber is phase 1 of a new environmentally friendly energy plant currently being designed, for installation at EGGER UK’s chipboard manufacturing plant in Hexham.
Central to the drying process, it will be predominantly powered by waste dust collected from the sanding process.
EGGER Hexham’s current 50Mw energy plant, commissioned in 2008, generates 35MW of hot gas to remove moisture from woodchips and 15Mw thermal oil heat transfer. It currently uses wood-based material unsuitable for chipboard production as a fuel.
The new vertical firing chamber will house a modern, efficient 25Mw burner, while thermal oil heat from the current energy plant will be incorporated into a new steam turbine plant heat transfer system, which is non-hazardous and environmentally friendly.
Francis Brown fabricated the vertical firing chamber at its Stockton-on-Tees facility to tight dimensional tolerances and the project was delivered on time and to budget. It was recently installed following the completion of foundation works.
Duncan Warriner, Managing Director of Francis Brown, said: “The fabrication of the 32-ton vertical firing chamber marks a historic milestone in our 120-year journey. As an independent company, it exemplifies our unwavering commitment to precision and innovation, and I’d like to thank the team for their expertise and attention to detail. Francis Brown is proud to play a part in EGGER UK’s vision to create a more sustainable future.
“This is also an example of the high calibre of projects we are securing, which is evident in our growing order book for 2024, which is also creating the opportunity to create new jobs across the business.”
Arthur F. Harvey, EGGER UK Specialist Project Engineer, said: “It was important to find a company with the expertise and large workshop, to enable the accurate manufacturing of the chamber. Working with Francis Brown’s project team was a great collaboration, and they proved to be a super team. This was a very large item, which had to be manufactured to small tolerances. Francis Brown’s team rose to the challenge and successfully delivered what we required, on plan and on budget.”