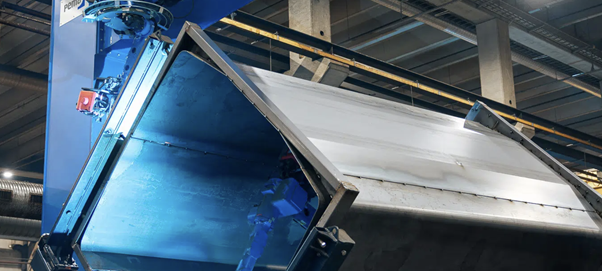
Leading the way with PEMA robotic solution
The Nordic leader in waste compactor manufacturing, Europress, has chosen the PEMA robot welding station to support its Lean-based production focused on efficiency.
Waste containers for different waste fractions are familiar to everyone. While some inefficient, open-top containers are still in use, closed waste containers equipped with hydraulic compactors are rapidly gaining market share. A new PEMA robot station, dedicated to welding these compactors, is now up and running at Europress’s factory in Kerava, Finland.

Europress chose the PEMA solution based on references from demanding, production-critical projects. Pemamek was also able to integrate the existing welding robots into the PEMA WeldControl software.
How can production be further optimized? How can energy efficiency be improved? And how can profitability and growth be secured at the same time?
At Europress, the path to optimization is guided by two key principles: the Lean manufacturing philosophy and production automation. In short, Lean aims to optimize all available resources to maximize customer value. Production automation, on the other hand, is particularly evident in welding operations.
Europress introduced its first welding robot in 2010. Since then, robotic solutions have also been adopted in shot blasting. The latest addition is the PEMA robot welding station, installed in 2023. In total, the company now operates six different robot stations.

Consistent quality with PEMA
Europress’s PEMA station features two robots welding simultaneously. While one robot welds the outer frame of the waste compactor, the other handles the interior and rear door. The frame being welded is mounted on a large PEMA positioner table that can rotate workpieces up to seven meters long according to the programmed instructions.
Previously, this phase required four welders working in two shifts. The welding positions were demanding and physically strenuous. Now, the welders utilize their expertise as robot operators and handle only a few finishing welds.

“In welding automation, Europress relies on market leader Pemamek. In return, Pemamek’s recycling solutions come from market leader Europress.” – Timo Huhtala, Executive Vice President, Europress
The secret lies in the software
The PEMA robot welding station is powered by the PEMA WeldControl 300 software, which includes an Offline feature. This feature allows programming of the next workpiece while the robots are still welding the current one.
In practice, hardly any programming is required at this stage, since the welding paths for dozens of compactor models are already pre-programmed. The operator simply selects the correct model and starts the robot using the PEMA CellControl interface.
Robot programming is smooth, and the Offline feature significantly reduces downtime. The PEMA station already handles the welding of most waste compactor models and aligns well with Lean manufacturing principles.
