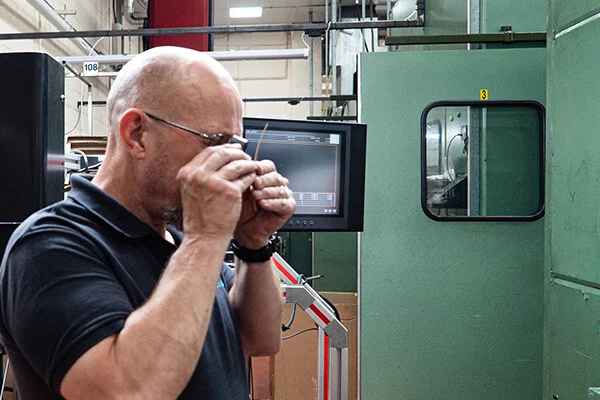
As demand increases for smaller, more efficient devices, there has been a similar move towards higher precision-stamped components. these two right, whilst maintaining competitive pricing, can be difficult for both manufacturers and suppliers. It but it is essential for the success of modern electronic products.
The Role of Precision Stamped Components in Electronics
Precision stamped components make up a large part of the manufacture of electronic devices, from consumer electronics like phones and computers to more specialised applications in transport and medical devices. These components, which often include connectors, terminals, shields, and other metal parts, must be produced with a high degree of accuracy to ensure they work as they should. Even minor deviations can lead to malfunction, decreased performance, or, in worst-case scenarios, product failure.
The need for precision is underscored by the increasing miniaturisation of electronics. As devices become smaller and more compact, components must also shrink without compromising functionality.
Key Factors Influencing Quality in Precision Stamping
Several factors influence the quality of precision-stamped components, from the design and manufacturing process to the materials used. Each step plays a role in making sure the final component meets the necessary specifications.
Stamping tools must be designed and maintained to exacting standards, as even slight wear or misalignment can result in defects. Regular inspection and maintenance of these tools are essential to maintain their accuracy, ensuring consistent quality across production runs.
Material selection is another critical aspect. Properties of the material being stamped can have a significant impact on the final component’s performance. In the electronics industry, materials must often meet specific requirements for conductivity, durability, and resistance to environmental factors such as heat and corrosion. The choice of material should be made with the end application in mind, balancing performance with cost to ensure that the component meets both functional and comes in within budget.
Finally, the stamping process itself must be closely controlled to ensure quality. This includes monitoring key parameters such as press speed, force, and temperature, as well as inspecting components at various stages of production to catch any defects early. Advanced techniques such as statistical process control (SPC) can help manufacturers maintain tight tolerances and prevent defects from occurring.
Achieving Competitive Pricing Without Compromising on Quality
Manufacturers must find ways to control costs without sacrificing the precision and reliability of their components. This requires a multi-faceted approach, combining process optimisation with smart material selection and strategic supplier relationships.
One of the most effective ways to achieve cost savings is through process optimisation. By streamlining production processes and minimising waste, manufacturers can reduce costs while maintaining high standards. Automation plays a key role in this, allowing for faster, more efficient production with fewer errors. Modern stamping presses equipped with sensors and monitoring systems can detect issues in real-time, preventing defects before they occur and reducing downtime.
Material Matters
While high-performance materials may be necessary for certain applications, in other cases, alternative materials can provide similar performance at a lower cost. Working closely with material suppliers and leveraging their expertise can help manufacturers identify the best materials for their needs, balancing cost with performance to achieve optimal results.
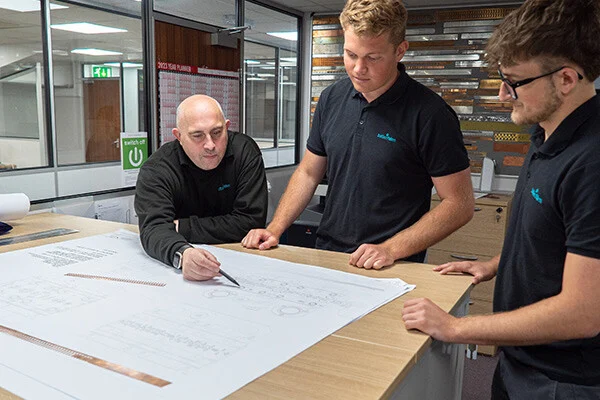
Collaborating can also help manufacturers secure better pricing. Suppliers with extensive experience in precision stamping for the electronics industry can offer valuable insights into cost-saving opportunities, such as bulk purchasing agreements or long-term contracts that lock in favourable pricing. In addition, manufacturers can benefit from working with suppliers who offer value-added services such as design assistance, prototyping, and testing, which can help reduce the time and cost associated with bringing new products to market.
The Importance of Quality Control
In-process inspections help to catch defects early, before they can affect an entire production run. This might include visual inspections, dimensional measurements, or more advanced techniques such as x-ray or ultrasound testing, depending on the component’s complexity. By identifying issues early, manufacturers can adjust the process and prevent further defects.
Final testing is equally important, ensuring the finished components meet all functional and performance requirements before they are shipped. This might include electrical testing to ensure proper conductivity, as well as environmental testing to ensure that products can withstand the conditions they will face in use, such as extreme temperatures, humidity, or mechanical stress.
Through a combination of process optimisation, careful material selection, and rigorous quality control, manufacturers can achieve the perfect balance between quality and cost, delivering components that meet the needs of today’s electronics industry without breaking the budget.