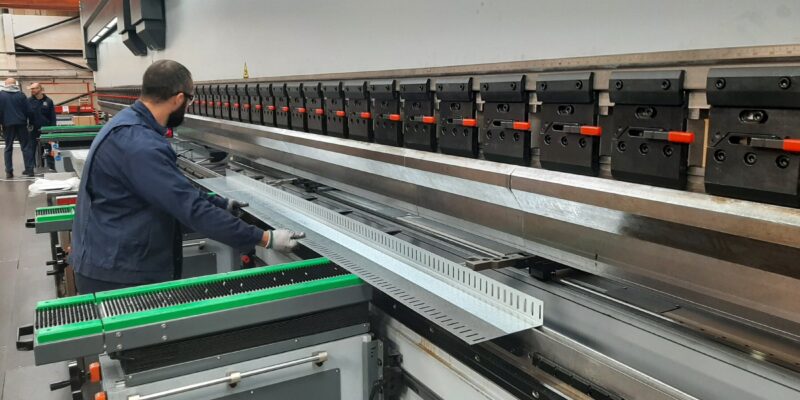
Ayrshire Metals Ltd, a leading manufacturer of cold-rolled sections for the construction industry, has invested in an impressive 14m-long, 640-ton ACCURL 6+1 axis tandem press brake from Axe & Status. Featuring an extensive range of advanced features, the new ACCURL press brake is raising productivity, quality and traceability to new levels at this progressive and ambitious manufacturing business.
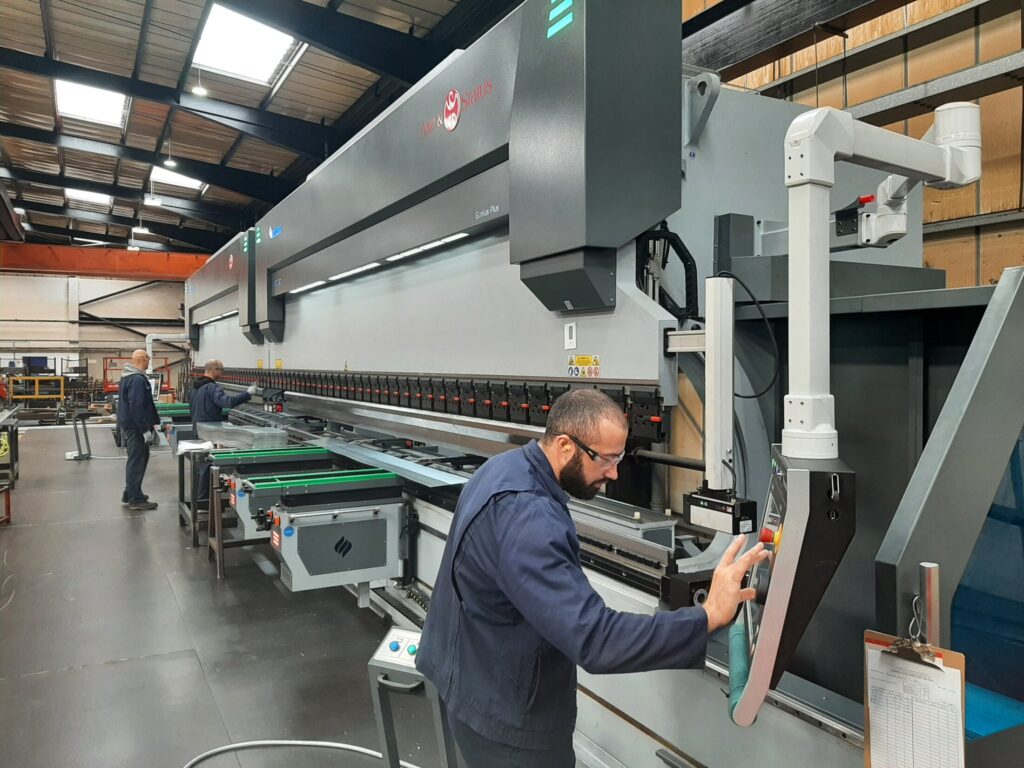
The Ayrshire Group can trace its origins back to the 1800s, when it was largely a manufacturer of ships on the west coast of Scotland. The company has come a long way since then and is now a leading manufacturer of cold-rolled sections at its 6.5-acre owner-occupied site in Daventry, Northamptonshire. The ISO9001 and CE/CA accredited company, which also has a subsidiary Sales and Technical office in Munich, Germany, manufactures most of its product range from S450 zinc-coated galvanised steel.
Five main product groups comprise the vast majority of manufacturing output. While traditional business at Ayrshire Metals is purlins/rails, the company also manufactures mezzanine floors, load-bearing steel framing systems and proprietary products like its AyrFrame™ lightweight, high-strength modular system and SwagBeam™ portal frame building system.
Out with the old
Until recently, Ayrshire Metals relied on a press brake that had been running since 1996. With machine reliability levels falling, the company decided it was time to invest in a new resource. Indeed, the new press brake is part of a five-year planned investment programme at Ayrshire Metals.
“Rather than replace like-for-like, we wanted a slightly bigger press brake to provide more capacity in both length and thickness,” explains Managing Director Scott Reilly. “We looked at three potential suppliers, but the responsiveness of Axe & Status caught our attention. Not only was their communication very clear from the outset, but Axe & Status also grasped the urgency of our situation as it wasn’t economic to keep repairing our existing press brake. Another major influence on our purchase decision was the value for money offered by the ACCURL press brake against competitor machines.”
The ACCURL tandem CNC press brake from Axe & Status arrived in June 2024, with machine operatives at Ayrshire Metals immediately commencing a programme of training.
“As you can image, the new ACCURL is very different to our existing 28-year-old press brake,” says Scott. “It’s akin to moving from a DOS operating system to Windows, such is the contrast. We can now use the DELEM® DA66T 2D graphical/3D visualisation touchscreen control to draw the required profile at the press brake without having to create a program manually. The difference is night and day.”
Playing the long game
The ACCURL has also increased production capability at Ayrshire Metals. The company is today able to bend lengths up to 14m, compared with 12.6m previously. In addition, whereas its existing press brake is on the limit when bending metal at 3mm thick, Ayrshire Metals can now form sheet up to 4mm thick across material up to 14m long. For shorter lengths it is possible to bend much thicker material.
“We’re hoping this extra capability will allow us to access new markets. At the moment, we focus solely on construction products for buildings, but starting from 2025 we want to explore sectors outside of our traditional comfort zone.”
All products at Ayrshire Metals are made to order. The company holds no stock and there is no minimum order.
Says Scott: “While we make our high-running products on a rolling mill, the ACCURL gives us the flexibility to manufacture bespoke items. Compared with our existing press brake, we now enjoy more productivity and far greater reliability. Moreover, our uptime is 100% compared with around 70% previously. Speed of response is vital in the construction sector and we’ve seen a big boost in machine availability and OEE (overall equipment effectiveness).”
Ayrshire Metals runs two shifts (day and night). Depending on workload, the company has the option to run its ACCURL press brake around the clock if necessary.
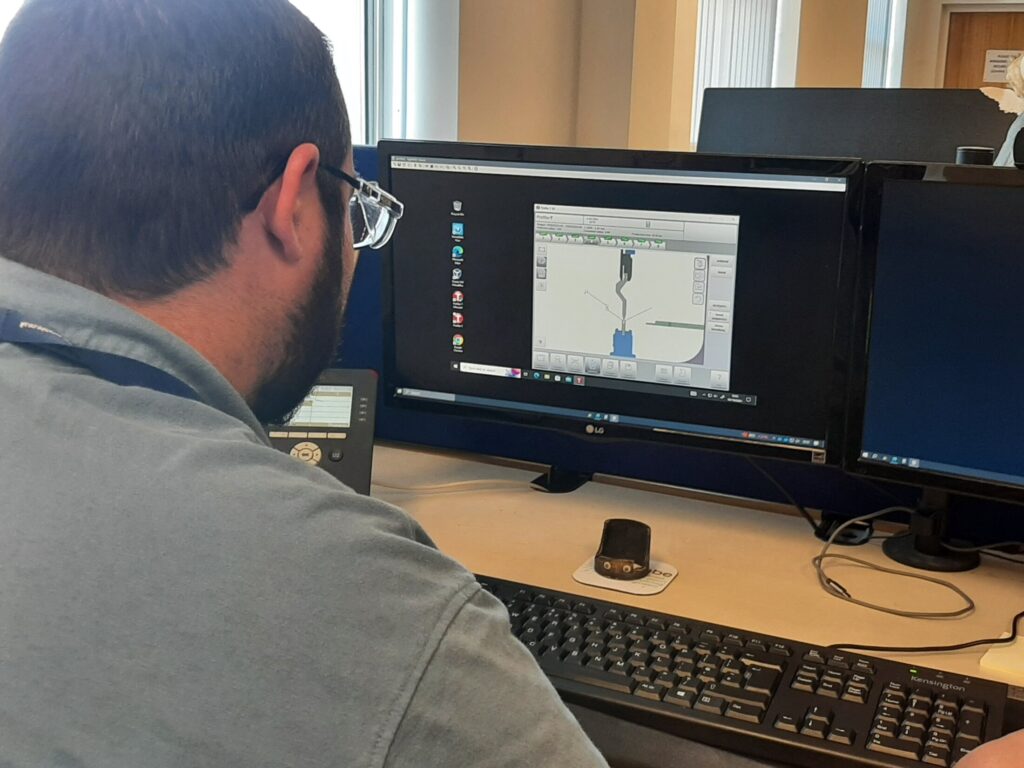
The price is right
“The construction market is very price-sensitive, both here in the UK and in mainland Europe, where we export around 50% of production. There’s very little loyalty. So any advantage in productivity and/or efficiency will help us remain competitive and potentially improve our margin, which is vital for the future of the business.”
The 14m, 640-ton ACCURL servo-hydraulic tandem press brake at Ayrshire Metals features a throat depth of 750mm and Y1, Y2, X, R, Z1 and Z2 axes. The company can switch quickly between tandem or single-mode operation at any time, and transfer bending programs between the two presses. Among many notable features is high dynamic Y-axis control for over 30% higher productivity. Further features include LAZERSAFE® light guard systems, Wila crowning, quick-release clamping, a LAZERSAFE® LZS-XL system with tandem adaptor system, CE and CSA-certified LAZERSAFE®-embedded IRIS block laser, and AP01-AP02 sheet followers.
Ayrshire Metals also has two licenses of ACCURL’s DELEM® TL offline software, one at each of its technical offices in the UK and Germany. The company can seamlessly send fully simulated and tested data files between facilities. It is now implementing full networking in support of direct file transfer to the press brake.
“Skills remain a big issue,” states Scott. “A major advantage with our ACCURL press brake is the ease of training operators. If you can draw a profile, you can program the machine. It was a big selling point.”
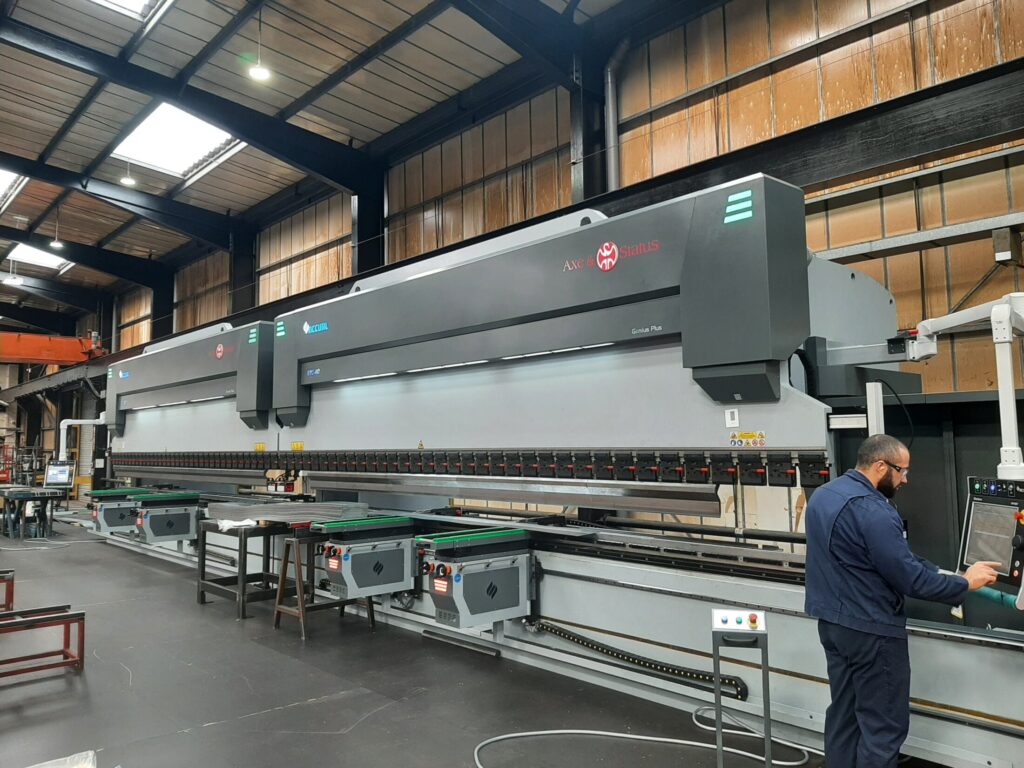
Growth opportunity
Generating annual turnover in the region of £20 million with 60 employees in the UK and a further 20 in Germany, Ayrshire Metals wants to build on its success with further growth. And the best way to meet this ambition is through investment.
“We’ve been around for many years and it’s easy to carry on as normal,” says Scott. “However, you sometimes need to take a step back and see what new manufacturing technologies are available. It’s about improving our capabilities and efficiencies to provide customers with the best value possible. With our ACCURL press brake we are more productive, more accurate and have much better traceability. All of these factors benefit our customers.”
With features such as the ACCURL Hybrid Servo ECO function and IE3 class high-efficiency motor, the environment will also benefit.
“It’s too early to say, but we’re expecting a sizeable percentage reduction in energy consumption. We’ve started our journey to net zero, so any carbon footprint reductions are very welcome.”
ACCURL tandem press brakes from Axe & Status are available up to 6000 tons capacity and 24m in length, with support from comprehensive warranty and service packages. A three-year arrangement is in place with Ayrshire Metals, for example.