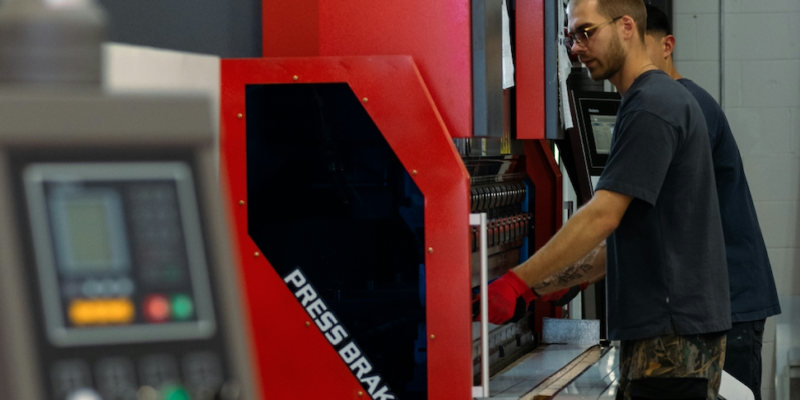
Energy efficiency is no longer just an environmental concern — it’s a bottom-line issue that determines which manufacturers thrive and which fall behind says Adrian Wright from Daltons Wadkin
In an era where manufacturing efficiency is more crucial than ever, businesses across the industry are looking for ways to reduce costs, minimise waste, and enhance productivity.
Automation and Industry 4.0 have become buzzwords as well as dominant trends, with manufacturers increasingly integrating robotics, data-driven decision-making, and smarter machinery into their processes.
It was expected that by 2025, 50% of manufacturers globally were expected to adopt IoT technologies as part of their Industry 4.0 strategies. This adoption is driven by the potential for productivity increases of 20–35% and downtime reductions of up to 50%.
However, one aspect that often gets overlooked in these discussions is energy efficiency — an area where modern CNC routers and fiber lasers are redefining what’s possible.
The truth behind the hidden costs of waste in manufacturing
Waste reduction is an ongoing challenge in manufacturing. While many businesses recognise the importance of optimising efficiency, few fully quantify the financial and environmental cost of material waste.
Daltons Wadkin, a UK leader in implementing precision-driven CNC and laser solutions to cut waste, recently approached about improving accuracy and driving efficiency gains. They were discarding 20% of parts for every 1,000 produced, meaning 200 parts per batch were going straight to waste. In another case, a company using a particular optical measuring system found that only three out of 16 precision blades met the required tolerances, resulting in a staggering 75-80% scrap rate.
These inefficiencies aren’t just costly in terms of raw materials; they also have a direct impact on operational costs, including machine running times, energy consumption, and additional labour. Data shows companies can spend between 4–10% of their annual turnover on waste if they lack proper waste management strategies that focus on minimisation and recycling.
Industry reports suggest that manufacturing waste accounts for billions in losses annually. According to a report by the manufacturing industry generates around 17% of global waste, further exacerbating supply chain constraints and environmental impact.
So, what are the modern energy-efficient alternatives
Traditional manufacturing processes often rely on outdated machinery with high energy consumption and inconsistent performance.
In contrast, modern CNC routers have been engineered to optimise material usage, improve accuracy, and significantly lower power consumption.
One of the primary advantages of CNC routers in multi-material manufacturing is their precision. By reducing deviation in cuts and machining, CNC routers minimise scrap, leading to both cost savings and sustainability benefits.
In a competitive landscape where some brands are still playing catch-up in terms of repeatability and efficiency, investing in high-precision solutions offers businesses a significant competitive edge.
Furthermore, CNC routers integrate seamlessly with smart factory systems, offering real-time data insights on energy use, maintenance needs, and material efficiency. This aligns with the wider shift toward Industry 4.0, where manufacturers are leveraging data and automation to refine their processes and drive productivity gains.
Energy efficiency in practice and its impact on the bottom line
Beyond material savings, modern CNC routers also offer substantial energy efficiency benefits. The shift towards leaner, greener machines is evident in the latest developments across the industry.
During a recent trip to Italy to visit Italian Press Brake supplier, Schaivi, the Daltons Wadkin team saw first-hand how important energy efficiency is in this highly competitive market. The point that has driven home of late to press brake users is how “fully” electric small and medium-sized machines are more efficient than “full” hydraulic machines and can be offered in higher tonnage by comparison. Smart automation is now also allowing press brakes to achieve job changeovers with zero operational setup time — a remarkable leap in efficiency
For manufacturers, the financial case for energy-efficient machinery is clear. The cost of running high-energy, inefficient equipment quickly adds up, especially when factoring in rising electricity prices and sustainability targets.
Companies that fail to adopt more energy-conscious machinery will find themselves at a long-term disadvantage, both in terms of cost and environmental compliance.
As manufacturers face growing pressure to cut costs while improving sustainability, those who invest in smarter solutions today will secure a long-term competitive edge.
The future of manufacturing can be smarter, leaner, and more sustainable
As manufacturing moves deeper into the era of automation and Industry 4.0, energy efficiency must be at the forefront of decision-making.
Investing in smarter machinery — whether CNC routers, fiber lasers, or automated press brakes — can yield significant long-term benefits, from reduced material waste to lower operational costs and increased competitiveness. Automation technologies such as IoT, machine learning, and cyber-physical systems can reduce energy consumption by up to 20% in manufacturing processes.
Many manufacturers still operate in a reactive mode, dealing with inefficiencies only when they become too costly to ignore. However, the businesses that will thrive in the future are those that proactively seek smarter solutions now.
It is becoming more prevalent than ever before that companies are transforming their production processes with more energy-efficient, precision-driven technology. Those who embrace these advancements will not only cut costs but also position themselves as leaders in sustainable manufacturing.
Final thoughts and takeaways
The energy efficiency revolution in manufacturing is here, but only those who take action will reap its benefits.
As automation, robotics, and data utilisation continue to define the industry, businesses must look beyond just acquiring new machinery. They need to invest in solutions that drive real, measurable efficiency and productivity gains — both in energy consumption and material usage.
Key takeaways for manufacturing leaders:
· Kimla CNC routers and fiber lasers can cut waste by up to 30% while reducing energy consumption.
· Smart automation can reduce job changeovers to zero operational setup time, boosting efficiency.
· Companies that invest in energy-efficient machinery will see long-term cost savings and regulatory compliance advantages.
The future of sustainable, cost-effective manufacturing is within every manufacturer’s reach. For those looking to stay ahead of the curve, now is the time to rethink their approach to efficiency. The right machinery is more than just a tool — it’s a competitive advantage from machines Daltons Wadkin see are the best machines in the market to achieve just that.