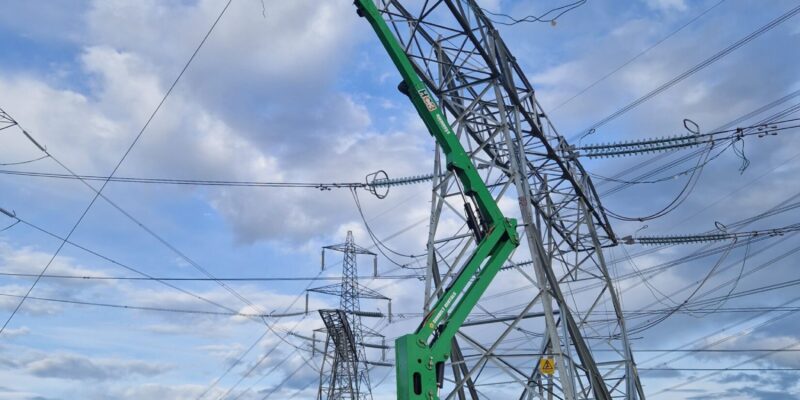
Had-Fab take pride in delivering top-quality steel fabrication solutions tailored to meet the complex demands of its clients. The company’s recent work on the East Coast Line power transmission project is a testament to their expertise, precision, and commitment to excellence.
This project involved the fabrication of multiple L8 towers, including terminal through line towers and regular in-line towers, demonstrating Had-Fab’s capability to execute large-scale infrastructure projects with meticulous attention to detail.
The Scope of the Project
The East Coast Line project was a significant undertaking, requiring the fabrication of several large L8 towers. These towers are critical components of the power transmission infrastructure, providing the necessary support for high-voltage transmission lines that deliver electricity across vast distances. Had-Fab’s role extended beyond just fabricating these towers; they also ensured that every piece fit perfectly on-site, facilitating a smooth and efficient installation process.
Key components of the project included:
- Fabrication of Multiple L8 Towers: Had-Fab fabricated both terminal through line towers and regular in-line towers, each designed to meet specific engineering and operational requirements for power transmission.
- Modified Stubs Setting Template: To ensure accurate installation on-site, they fabricated precise stub setting templates. These templates are crucial for positioning the towers correctly, ensuring perfect alignment to support the high-voltage lines.
- Check Erection at Had-Fab Facility: Before transporting the towers to the site, the team conducted a thorough check erection at our Had-Fab facility. This step was essential to confirm that all components fit together as designed, ensuring a seamless installation process in the field.
- Provision of ACDs (Assembly and Construction Drawings): they also provided detailed ACDs to guide the installation team, ensuring that each tower was assembled correctly and efficiently.
The Importance of Check Erection
One of the standout aspects of this project was the decision to perform a check erection of the towers at Had-Fab’s facility. This proactive approach allowed the team to identify and resolve any potential issues before the towers were transported to the site. By doing this, they ensured that the on-site installation would be smooth, efficient, and free of unexpected delays.
The check erection process involved assembling the towers exactly as they would be in the field, verifying that each component fits perfectly with the next. This step underscores Had-Fab’s commitment to quality and their understanding that in large-scale infrastructure projects, precision is paramount.
Delivering on Time and to Specification
The success of the East Coast Line project depended not only on the quality of Had-Fab’s fabrication work but also on their ability to deliver on time. Power transmission projects like this one operate under tight schedules, and any delays can have significant consequences for the broader power grid. Had-Fab understand these pressures and work diligently to ensure that their clients receive their components exactly when they need them, without compromising on quality.
Their ability to deliver high-quality fabricated towers on time and to specification played a crucial role in the successful completion of the East Coast Line project. The towers they provided are now integral parts of the power transmission infrastructure, ensuring the reliable delivery of electricity across the region.
Conclusion
The East Coast Line project is another example of Had-Fab’s commitment to excellence in steel fabrication. By combining engineering expertise with rigorous quality control processes, such as the check erection at their facility, Had-Fab were able to deliver a project that met the client’s exacting standards.