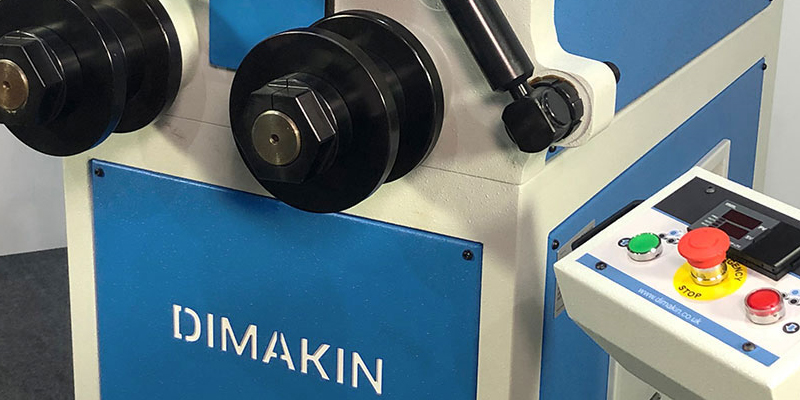
There are a few considerations to make when purchasing a roll bending machine. Getting the right machine not only for your current applications, but also forecasting for future growth, is of key importance. No one wants to buy a machine that is fit for only one purpose. Potentially leaving them requiring a second, or replacement machine, only a few months down the line. Because of this, it’s crucial to make these considerations at the front end of your purchase.
Below are three considerations to make when investing in a new ring roller. Hopefully it will help narrow down your options and support you choosing the right machine for you and your workshop!
Top roll descent or hydraulic top roll descent:
The first choice you’re likely to be making is between manual top roll descent and hydraulic top roll descent. This decision will primarily be dictated by the repeatability you wish to achieve. Small batches, bespoke bending, and one-offs can very often be eyeballed by the operator. Because of this, it is often possible to forgo the need for hydraulic top roll control.
However, should you be roll bending and require repeatability, hydraulic control is key! By implementing a hydraulic top roll position, and linking it with a digital readout (DRO), it is possible to achieve repeatable bends for years at a time. This repeatability even extends either side of other bending jobs. For example, you could note down the value of the descent, and move on to another job. Once you return to your previous bend, just by inputting your known value, the machine will produce the same bend!
Two driven rolls or three driven rolls:
From the first machine all the way to the RH-602, DIMAKIN roll benders come with two driven rolls (This can be noted by the last number in the model – RH-602). From here onwards, starting with the RH-603, the machines boast three driven rolls. Three driven rolls add an advantage to the machine that allows them to roll material and profiles at tighter radii.
Additionally, with two driven rolls, the tooling is required to be knurled to grip to the material. Three driven rolled machines, on the other hand, do not require the standard tooling to be knurled. Due to this, you might consider the finished product implications of tooling marking. Will the bend require some cleanup or finishing after a harsh bend? Is this acceptable?
Capacity for now, and for the future
By now we get to the most important aspect. Capacity. There are many, many things you can bend with a roll bender, sometimes called a section bender. Consequently, there are many, many specifications to contemplate. Try to consider more than the single application that drove you to need a bending machine in the first place.
If you’re looking to bend tube, also think about flat bar bending the hard way or the easy way. A new machine can open new doors and new business. Because of this you should keep in mind any new ventures that this machine could open. Additionally, you should also consider the application you’re currently using the machine for, but with more demand! Look for the machine that can give you the most in more ways that budget. For example, it may be more expensive outright, but will it triple your production rates, double your product range. It could also half your fabrication time!
By now I hope you have been able to consider which roll bending machine would be the best fit for your workshop. If, however, you still have any questions, just give us a call or email and we will be happy to help! Additionally, you can contact a live sales expert via the live chat option on any DIMAKIN webpage.