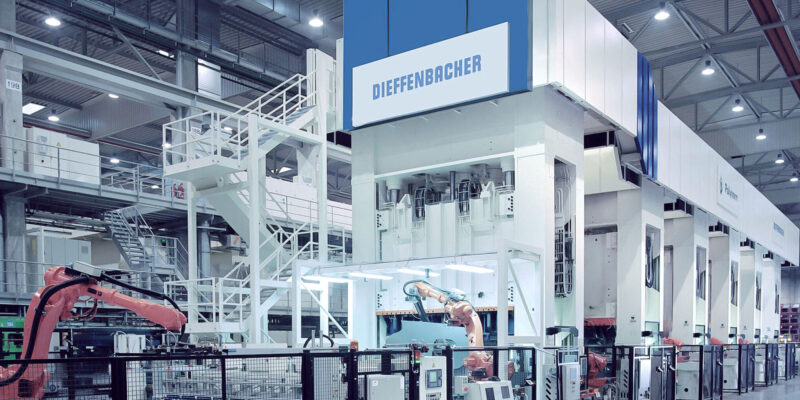
Companies interested in advanced system solutions for metal forming will find German machine and plant manufacturer DIEFFENBACHER primed to help them capture the power of productivity at this year’s EuroBLECH in Hannover, October 22-25.
At the booth co-hosted by the Wirtschaftsförderung Heilbronn-Franken in hall 27, booth E104, DIEFFENBACHER will showcase hydraulic forming presses and complete press lines for sheet metal forming and the production of high-quality stainless steel parts. Digitalization and sustainability solutions, along with service and automation expertise, will also be highlighted.
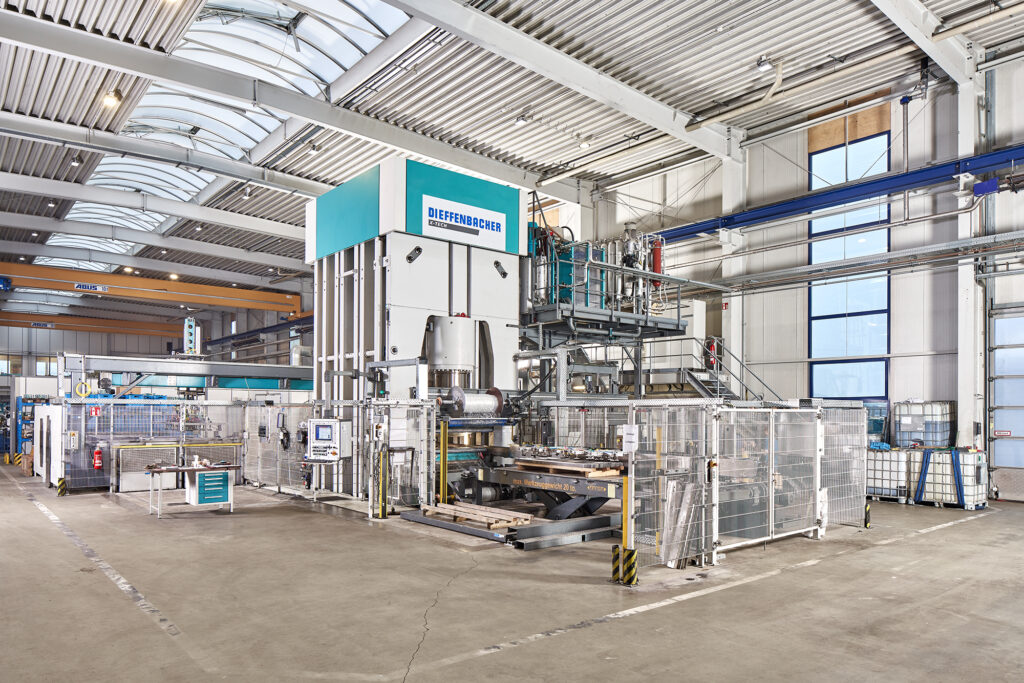
“One of our strengths is plant automation,” explains Georg Obermaier, Head of the Forming Business Unit at DIEFFENBACHER. “Our solutions with sophisticated gripper technology ensure short cycle times with perfectly coordinated processes. This increases productivity and ensures high parts quality. Our automation expertise applies to both new plants and existing production lines,” he adds.
“Our service portfolio will be another focus at EuroBLECH,” says DIEFFENBACHER’s Head of Service Alexander Ries. “In addition to spare parts supply and services such as repairs, process optimizations, safety checks and training, our digital services are constantly growing. They include the spare parts catalog MyDIEFFENBACHER Parts and our ticket system MyDIEFFENBACHER Messenger,” he explains.
“We’ll also present our modernization and conversion portfolio, highlighting our customer Thermowave, among others,” says Ries. In Berga, Germany, Thermowave manufactures plate heat exchangers using a DIEFFENBACHER plant with an X-Tech embossing press with a pressing force of 12,000 tons, a tool changing system and complete automation, including a blank loader. Because the hydraulic components Thermowave needed were no longer available, DIEFFENBACHER’s plant modernization plan included developing replacement valves that could economically return the machine to service. “DIEFFENBACHER met all our challenges, modernizing our press system to state-of-the-art capabilities through its partnership mentality and unwavering commitment,” says Thermowave Managing Director Clemens Starzinski.
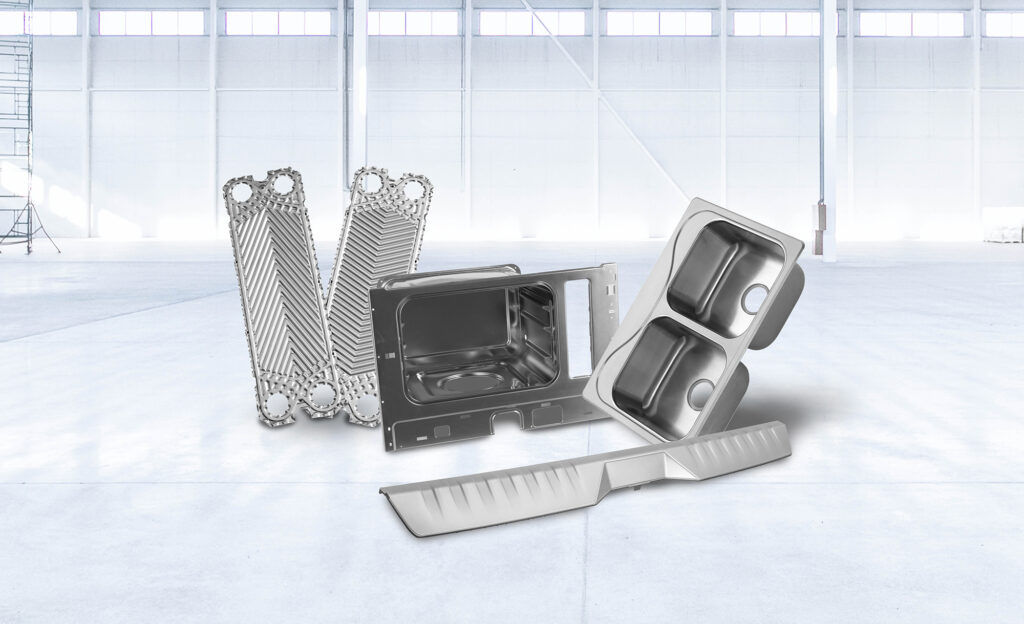
The megatrends of digitalization and sustainability go hand in hand at DIEFFENBACHER. With extensive diagnostic options, the EVORIS digitalization platform helps plant operators save energy and raw materials. For example, the EVORIS Reports app provides information about conspicuous deviations in production related to individual process parameters, overall plant performance and cycle time. The app also shows consumption values for the entire plant, highlighting anomalies between production output and energy consumption. The Anomaly Detection app detects deviations on all machines and plant components involved in production, which can then be counteracted in a targeted manner. For example, the production of defective products can be detected and avoided at an early stage.
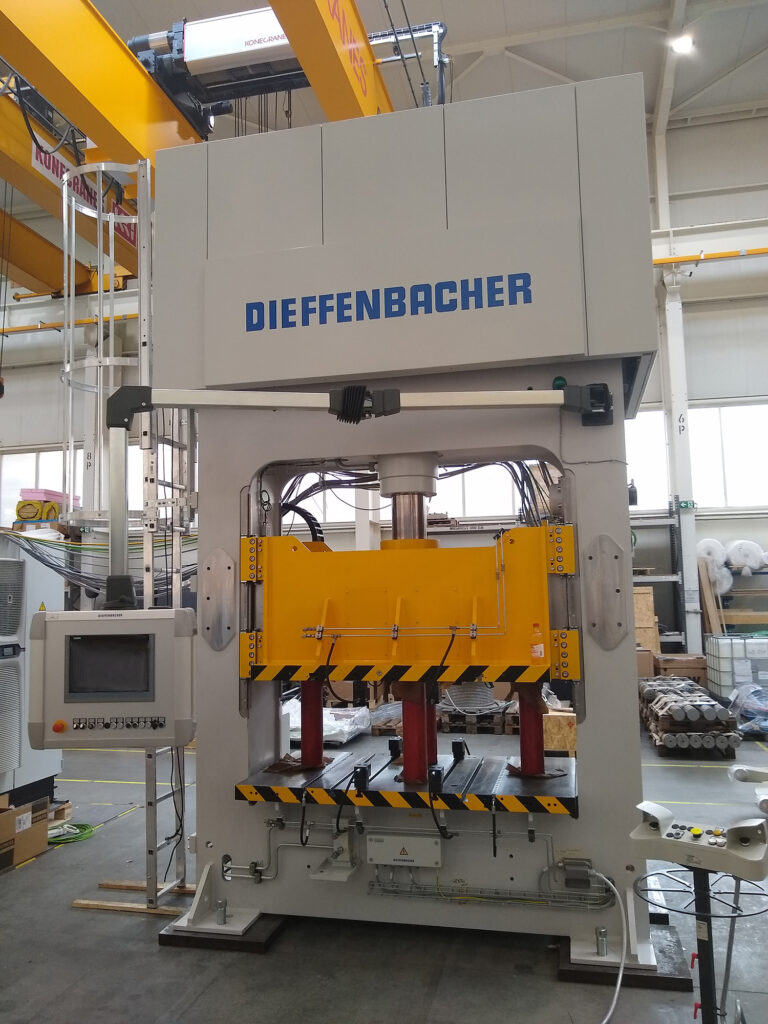
In addition, the TailoredPress, DIEFFENBACHER’s economical all-rounder with a highly attractive price-performance ratio, can reduce energy use by up to 70%, depending on the application. Variable-speed pump drives minimize unnecessary energy consumption, which can occur, for example, during loading and unloading, setup and maintenance of the press, and even in many phases of the normal press cycle. Control is fully automatic. The operator sets forces, paths and parameters as usual, and the required speed is automatically calculated and set. In this way, the pump always operates in an optimal range and works efficiently.
“Our smart concepts for saving energy and increasing material efficiency contribute to making our customers’ production processes more sustainable,” says Obermaier. “With flexible machine concepts and customized complete plant solutions—even for niche applications—we support customers in all phases of their projects, ranging from planning new press shops to integrating forming lines into existing structures,” he adds.
DIEFFENBACHER’s embossing press rounds out the company’s EuroBLECH presence. The high-performance complete system for stamping plates for stainless steel heat exchangers easily meets the high demands for accurate embossing depth. DIEFFENBACHER’s know-how ranges from the high-performance press to feeding and removal equipment to tools and tool-changing systems. The result is an optimal overall concept and fewer interfaces.
“We expect a great trade fair with lots of good conversations and exciting discussions with existing and new contacts,” concludes Obermaier. “Our entire team is looking forward to it.”