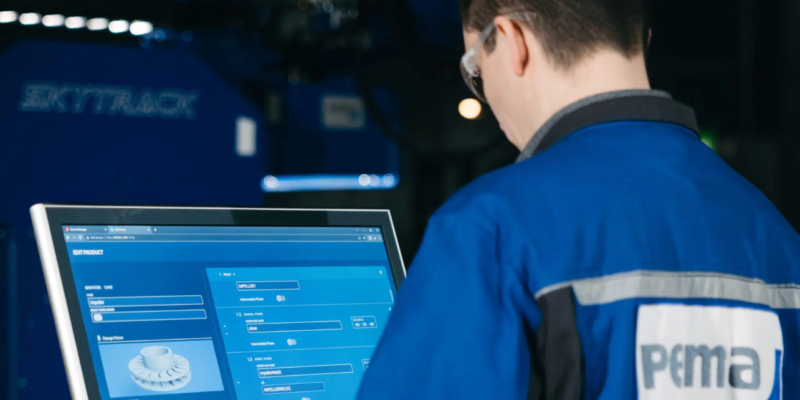
Custom robotic welding stations have the potential to revolutionize your production line but only if the investment is approached strategically.
As the demand for automation continues to rise, businesses in manufacturing are turning to custom robotic welding stations to enhance efficiency and stay competitive. These tailored solutions are designed to meet specific production needs, maximizing output and reducing waste. But making a successful investment in such systems requires careful planning, understanding of your operational goals, and consideration of long-term returns. In this guide, we’ll explore the key factors to consider when investing in custom robotic welding stations and how to ensure your decision drives profitability.
5 steps to a successful robotic welding investment:
The saying “Well planned is half done” applies also when investing in a robotic welding station. When the real need and demand are defined, the solution can be better designed to meet the customer’s requirements. Also, fast ROI will be achieved.
Thorough pre-design together with the supplier and purchaser.
- Collaboration with the vendor to design a system that meets operational requirements.
- Using simulations or prototypes to refine the design before full implementation.
Possible design changes in the products for example changing groove geometry or groove preparation method.
- Identifying necessary adjustments to the products or processes to ensure compatibility with robotic welding.
- Making strategic changes like altering groove geometry to maximize the effectiveness of the system.
Welding process evaluation and modification into robotic welding.
- Assessing current welding techniques and determining how to adapt them for automation.
- Ensuring the chosen process (e.g., MIG, TIG, or laser) aligns with long-term goals and can be scaled as needed.
Tailored and thorough training for all the participants.
- Developing customized a training program for operators and maintenance teams.
- Focusing on safety, troubleshooting, and operational proficiency to ensure seamless adoption of the new system.
Good level of maintenance and follow-up together with the supplier.
- Establishing a robust maintenance schedule to ensure the durability and efficiency of the system.
- Collaborating with the supplier for ongoing support and updates, ensuring the system stays optimized.
Well-designed robotic welding cells equal more productivity, better safety, high competitiveness, and fast return on investment. When robotic solutions are implemented well, they enable highly adaptive and efficient production. Welding robotic solutions are proven to increase the quality of finished products as well as the satisfaction of customers.