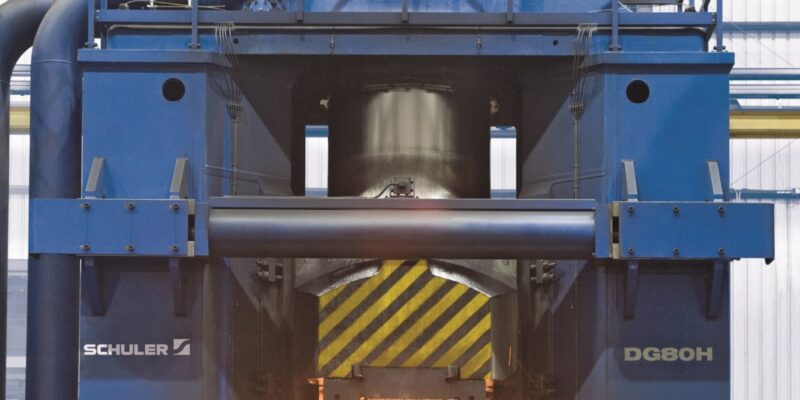
Large forged parts continue to be in high demand worldwide: The machine manufacturer Schuler has recently sold four BÊCHÉ counterblow hammers of all sizes. The applications of the forged parts are diverse and extend far beyond the drive train of trucks or ships: Products manufactured with the counterblow hammers also include parts for the oil and gas industry such as flanges or turbine blades for gas turbines or airplanes. The railway sector as well as the aerospace industry are also important customers.
“Our machines handle such challenging tasks with high repeat accuracy thanks to Schuler control,” explains Daniel Sauterleute, Sales Manager Forging Technology at the Göppingen world market leader in forming technology. The systems are both flexible and robust. “This also allows smaller batch sizes to be produced economically,” Sauterleute continues.
Schuler’s offering covers all relevant sizes. The range of counterblow hammers extends from small models like the DG 20 to the DG 140 with a working capacity of up to 1,400 kilojoules. The DG 20 offers a stroke per ram of 840 millimeters and achieves a maximum blow frequency of up to 45 per minute. The DG 140 has a striking force of 54,000 tons, a stroke per ram of up to 1150 millimeters, and a maximum blow frequency of up to 25 per minute.
The counterblow hammers are available in two series, HG and DG. The difference lies in the drive technology: The HG series, which is particularly suitable for the medium performance range, features a hydraulic drive. The DG series relies on the proven pneumatic drive, which enables the realization of very large forming energies. The stable frame design in combination with a massive guidance system ensures high precision in forging operations.
In addition, simulations can help customers optimize the forging process. Schuler has also developed a variety of solutions for networking forming technology, which increase productivity and availability. These include applications for monitoring operating conditions, press force, energy requirements, as well as cooling and lubrication circuits, “Track & Trace” for tracking components, or “Schuler Connect” for quick assistance in service cases using augmented reality technology.