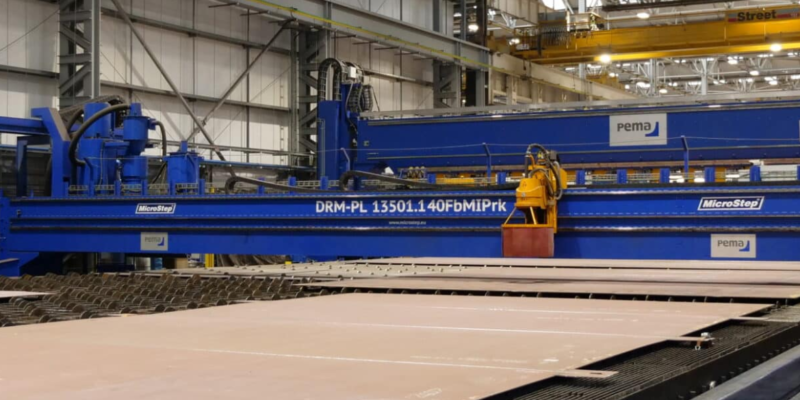
Babcock’s transformation into digital manufacturing hub
“As a leader in designing, building, assembling, maintaining, and upgrading international warships, this requires constant adaptation of advanced manufacturing techniques and continual development of our people, processes, and culture,” begins Joe, the Director of Operations at Babcock’s Rosyth site in Scotland.
Babcock is a leading provider of naval ships, offering whole life services including design, construction, assembly, maintenance, upgrades, repurposing, and through-life support for international warships. The company’s Rosyth site is one of the largest waterside manufacturing and repair facilities in the UK.
“We are a key supplier to the Royal Navy; hence we must deploy cutting-edge technology to deliver the quality standards and value for money required by them. In 2019, we were awarded the contract to deliver five Type 31 general-purpose frigates, which provides a significant opportunity for the historic Rosyth site.” Joe adds.
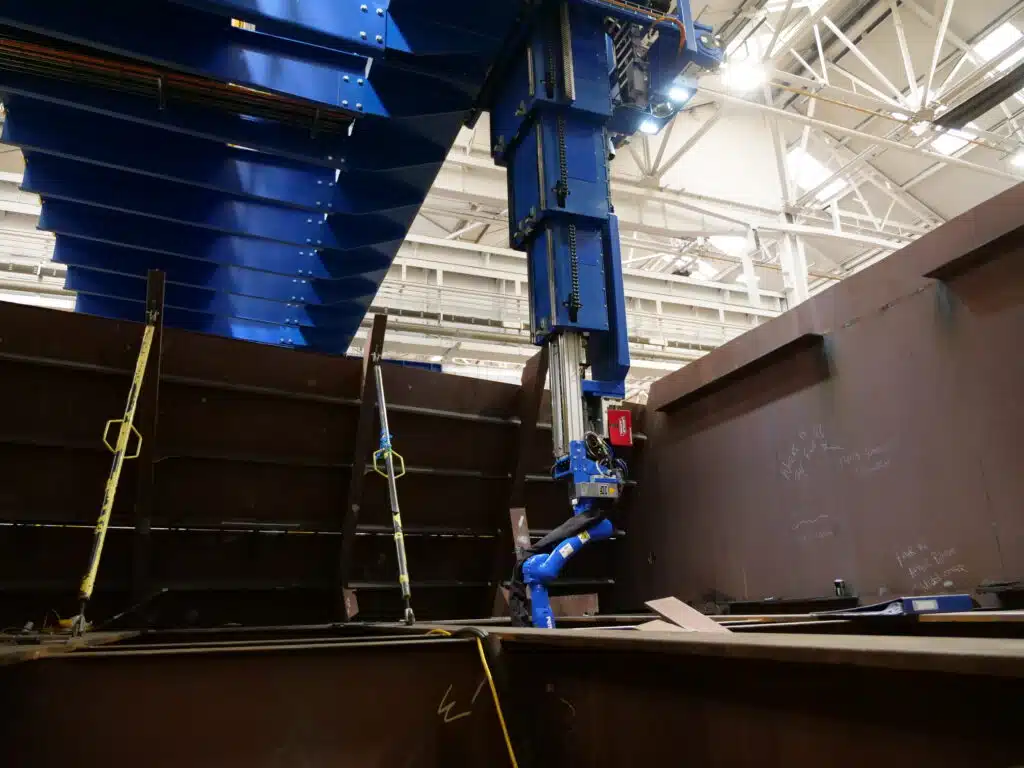
The Type 31 frigate programme
The ships, delivered under the UK’s National Shipbuilding Strategy, are state-of-the-art vessels designed to meet the challenges of today as well as have the flexibility to adapt to future requirements.
“Prior to Babcock securing the Type 31 programme, the company was responsible for the construction of circa 12,000 tons of steelwork for each of the Queen Elizabeth Class Aircraft Carriers (QEC),” Joe explains.
While aiming to meet the new manufacturing demands, Babcock saw an opportunity to enhance the Rosyth site’s long-term vision. As a result, the site underwent its most significant transformation yet –developing a digital manufacturing hub and creating a capability that will extend well into the future.
Joe continues, “Digital transformation is at the heart of the Type 31 programme, and PEMA shipyard automation has played a crucial role in Babcock’s transformation. We have invested more than £200m in developing the infrastructure at Rosyth to modernise the site for the QEC in which Babcock was a design and build partner with whole ship assembly taking place at Rosyth and of course our investment in infrastructure and facilities for Type 31 and beyond.”
By investing in technology and its people, Babcock is not only meeting the demands of today but also paving the way for the future of shipbuilding and the site’s success.
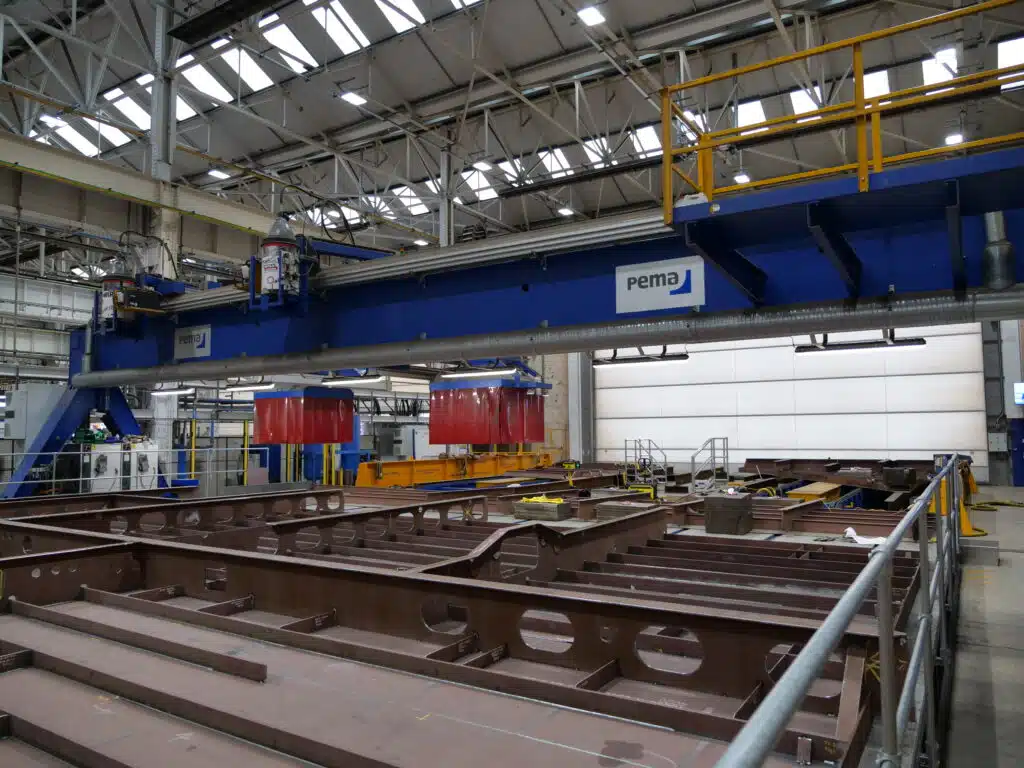
Advanced technology in action
In 2020, Babcock placed an order for three PEMA lines for automated panel production: PEMA Thin Plate Panel Line, PEMA Micro Panel Line, and PEMA T-beam Fabrication Line. Two years later, an additional unit line with PEMA robotic welding solution for open blocks was also ordered.
The lessons learned from the QEC program provided valuable knowledge on which manufacturing and assembly processes should be automated to ensure efficiencies and production quality from the outset. By automating panel, T-beam production, and unit construction, Babcock could focus skilled employees on more complex areas of shipbuilding and let the automation machines handle regular fitting and welding tasks.
When it comes to the most important developments, Michael, Head of Manufacturing, pinpoints the software capabilities and integration of 3D modeling with machine operations.
“The way we take the information from our 3D design model and convert it to information that the machines can work with is one of the most significant technological advancements,” Michael says.
The seamless transfer of data has significantly reduced lead times from engineering design to part production, ensuring consistency and precision.
Michael explains, “The software brings consistency in making sure that every part is in line with the design intent. There is no manual intervention because we’ve got that direct link from the 3D model right through to the machines on the shop floor.”
Pemamek’s in-house developed PEMA WeldControl 200, the software driving these advancements, is designed to enhance safety and reduce manual intervention.
“With safety at the heart of everything we do panels are moved by the automated material handling system, reducing the need for lifting and moving with cranes,” Michael notes.
The site automation lines not only mitigate safety risks but also boost productivity and quality.
“We can weld a bulb bar in 20 minutes, completely defect free. The transformation brought by the micro panel line has been particularly satisfying to witness,” Joe adds.
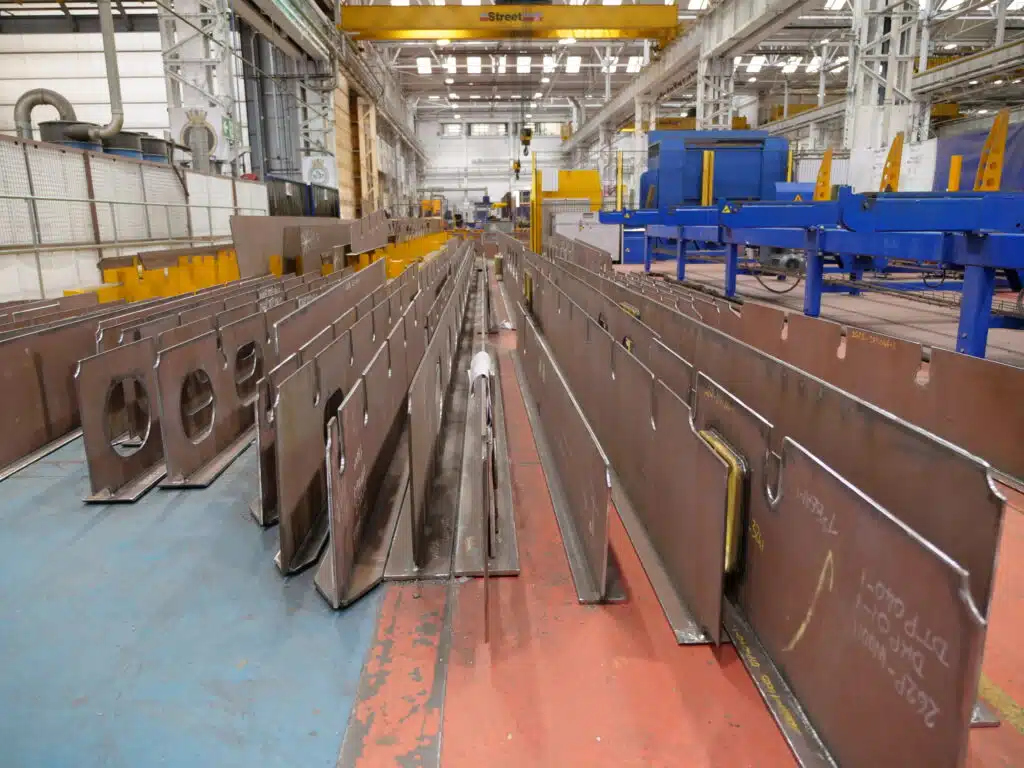
The best job ever
The scarcity of skilled welders is a challenge that a growing number of industries are facing globally. For example, it is estimated that by 2030, Australia will face a shortage of 75,000 welders and the US a shortage of 500,000. While the need for manufacturing is not decreasing, manufacturers are required to maintain and attract a workforce.
The impact of adopting automation technology on the workforce has been profound for Babcock, improving the company’s attractiveness as an employer.
“The consistency and quality control offered by automation minimizes defects, reducing the need for rework and corrections, and enhancing job satisfaction. Quite regularly you’ll hear the statement from those employees upskilled to work on the panel line that it’s the best job they’ve ever had,” says Joe.
The sense of pride among the team is visible: Joe continued: “The team is immensely proud of the products they’re building and the machines they operate. This transformation has been essential in addressing the challenge of skilled labour shortages and optimising the production process.”
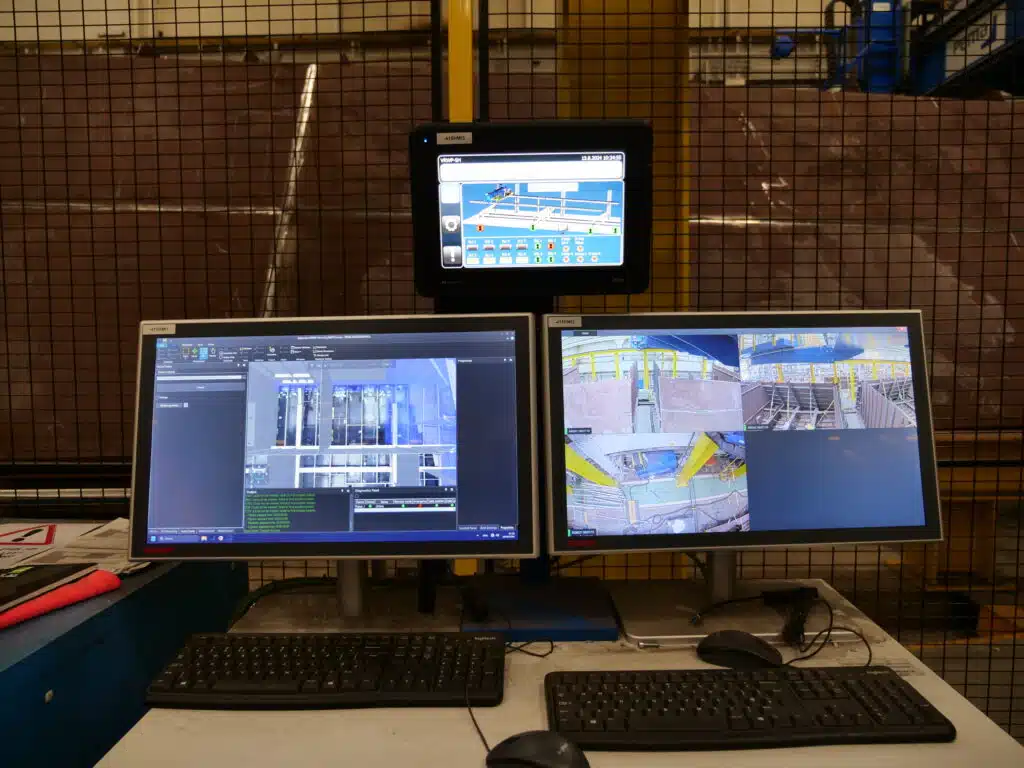
Looking ahead: Expanding opportunities
As Babcock continues to evolve, the focus remains on quality, safety, growth and capacity expansion.
“We’re looking at opportunities in the pipeline for how we can grow, expand, and increase capacity. Our collaboration and communication with Pemamek are ongoing. I think it is a win-win situation for both Babcock and Pemamek,” Joe says.
By investing in technology and its people, Babcock is not only meeting the demands of today but also paving the way for the future of shipbuilding and the site’s success. This vision advocates for advanced manufacturing techniques and a forward-thinking approach.
“Creating the digital manufacturing hub has been absolutely transformational for our business, and PEMA solutions have been at the heart of that,” Joe concludes.