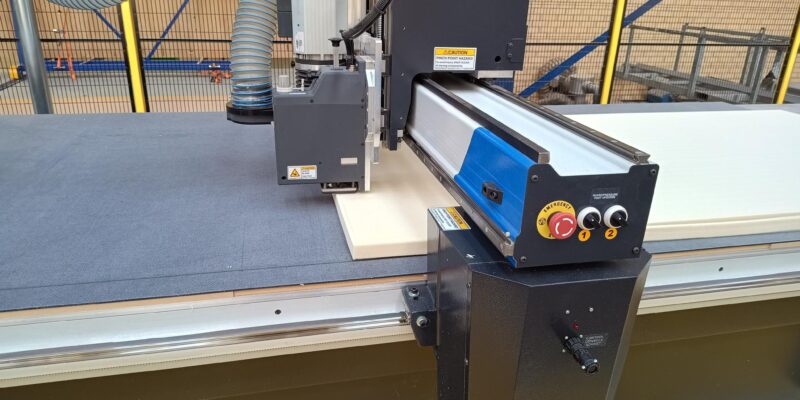
Auto-Trail V.R. Ltd is a distinguished British motorhome and campervan manufacturer, with a rich history dating back to 1982. Originating as a caravan repair business, Auto-Trail has evolved into a market leader, known for its customisable, high-quality leisure vehicles. This case study examines how Auto-Trail V.R. Ltd has implemented AXYZ’s advanced CNC routing technology to transform its manufacturing process, resulting in increased efficiency, reduced waste and enhanced product quality.
Company Background
Auto-Trail V.R. Ltd began as a caravan repair business but quickly evolved into a motorhome manufacturer, responding to growing customer demand for bespoke, luxury vehicles. Throughout the decades, from introducing the Cheyenne range in the 1990s to launching their first A-Class motorhome in 2006, Auto-Trail has been at the forefront of motorhome design and functionality.
A Journey of Exploration and Discovery
Auto-Trail offers more than just motorhomes; they provide a gateway to exploration and discovery. Each vehicle is designed to integrate seamlessly into the lifestyle of adventurers, enabling them to create lasting memories. Auto-Trail stands out in the motorhome industry for its commitment to personalisation, offering an extensive range of customisation options. This dedication ensures that each vehicle not only meets but exceeds customer expectations.
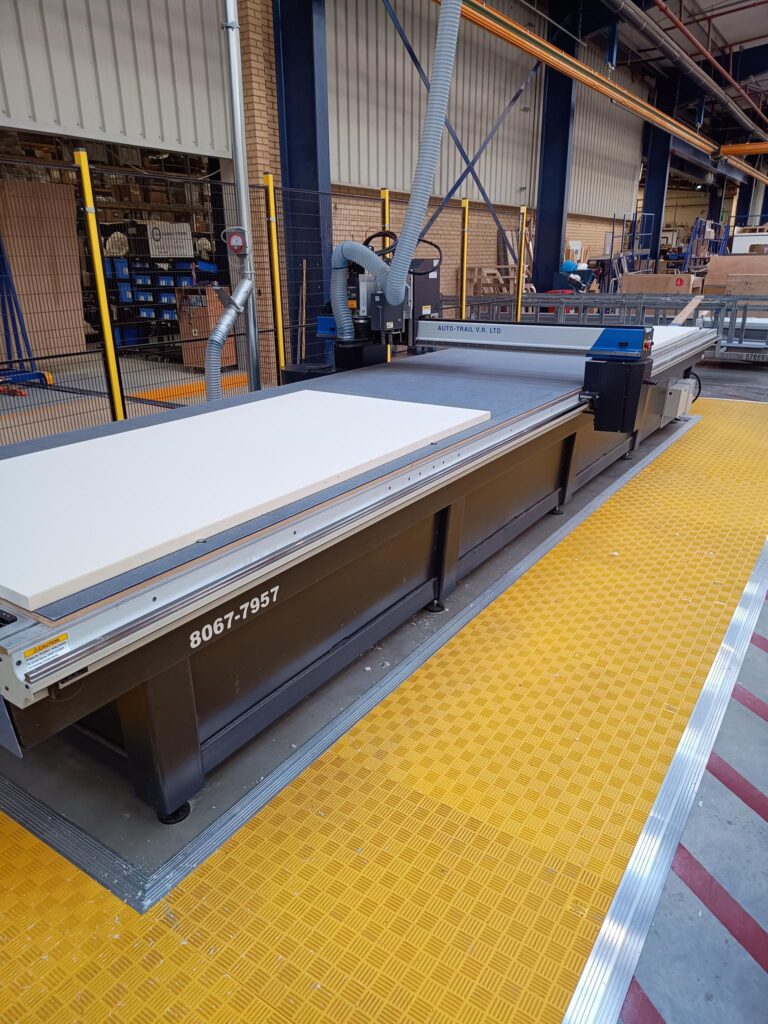
Adoption of AXYZ Technology
“In early 2024, facing the upcoming retirement of a skilled employee and the limitations of manual production methods (including hand-cutting from drawings and patterns) Auto-Trail decided to automate their manufacturing process” said Paul Spivey Design Engineer. This decision was also driven by the need to streamline operations and maintain control over material use, which manual methods could no longer efficiently support. Auto-Trail therefore decided to invest in AXYZ routers to automate its manufacturing processes. The adoption of CNC technology offered greater control over materials, improved design flexibility and enhanced production efficiency. After considering various options (including waterjet technology which proved to be logistically not viable) and the need for precise cuts, led them to explore other options, culminating in the selection of AXYZ’s CNC knife cutter. “I looked at several different manufactures, but AXYZ gave us the flexibility we were looking for with the ability to have a multi change router head and suitability for the manufacturing environment” said Paul Spivey.
Auto-Trail chose the AXYZ INFINITE 4022 1C2Z ATC CNC Router. The INFINITE router is a highly configurable CNC machine that is suitable for one-off, small batch production as well as high volume and high productivity applications, including woodworking, plastic fabrication, engineering plastic machining and so much more. For a wide range of routing operations, one can choose from high-speed spindles ranging from 5HP to 15HP. For knife cutting, choose from a tangential knife, which can be used for creasing and folding applications or an oscillating knife which can be used to process soft goods material.
The Role of AXYZ Machines in Auto-Trail’s Manufacturing
The AXYZ machines revolutionised Auto-Trail’s production processes, particularly in handling insulation material for pressed panels. Instead of manual cutting, CNC routing enabled precise shaping, reduced component count per panel, improved fit and reduced waste, printing, paper and transport costs. Additionally, the machines facilitated the production of customised parts specific to vehicle models, enhancing overall efficiency and material utilisation.
The integration of AXYZ routers at Auto-Trail has also enhanced design and production. The CNC technology has enabled complex cuts, reducing the need for plywood patterns and the number of components per panel from ten to four. This has streamlined the assembly process significantly.
The improvement in fit of components, due to the precise cutting ability of the AXYZ machines has led to less rework and errors, resulting in a reduction in the labour intensity. The automation of cutting processes has descaled the skill requirements, allowing less skilled workers to manage operations efficiently, which is vital as the workforce ages.
Quality and Innovation
The integration of AXYZ technology has not only optimised production but also maintained, if not enhanced, the quality of the final products. The precision of the AXYZ routers ensures each part meets strict quality standards, which is crucial for the overall reliability and performance of Auto-Trail’s motorhomes.
Cost Savings and Quality Improvements:
The adoption of AXYZ machines resulted in significant cost savings and quality improvements for Auto-Trail. By optimising material usage, reducing waste and enhancing panel construction, the company achieved measurable efficiencies in production. Furthermore, the precision and accuracy afforded by CNC routing translated into superior product quality, reinforcing Auto-Trail’s commitment to excellence and customer satisfaction and reinforcing Auto-Trail’s reputation for excellence.
Employee Engagement and Job Satisfaction
The introduction of automation at Auto-Trail elicited positive responses from employees, who viewed it as an opportunity for professional growth and skill development. Rather than displacing workers, the integration of AXYZ machines empowered employees to adapt to new technologies and enhance their roles within the organisation. As automation freed up time previously spent on manual tasks, employees could redirect their efforts towards innovation, collaboration and continuous improvement.
While the current workforce size remains stable, the skill requirements have evolved. Auto-Trail has invested in training and development to ensure employees are well-equipped to operate the new technology efficiently.
Challenges and Solutions:
The integration of AXYZ machines presented Auto-Trail with several challenges, including spatial constraints and process optimisation. However, through meticulous planning, iterative testing and collaborative problem-solving, the company successfully overcame these obstacles. Specialised equipment, such as customised cages for transporting parts and comprehensive adjustments to bills of materials (BOMs), cut lists and drawings ensured a seamless transition to automated production.
Maintenance and Future Integration:
Auto-Trail ensures the smooth operation of AXYZ machines through regular maintenance by onsite engineers and a maintenance contract with AXYZ. Looking ahead, the company remains committed to further integrating automation into its processes, continually evaluating opportunities to optimise production and drive innovation.
Future Prospects and Automation Plans
Auto-Trail V.R. Ltd is continually assessing and integrating automation into their production processes. The company plans to expand the use of automated technologies to enhance other areas of production, aiming for greater efficiency and productivity.
Conclusion
The implementation of AXYZ machines went beyond mere automation; it ushered in a paradigm shift in how Auto-Trail approached its manufacturing processes. Beyond the initial task of replacing manual cutting of insulation material, the CNC routers enabled the company to reimagine its entire production workflow. By embracing CNC technology, Auto-Trail gained the flexibility to create custom-shaped parts, optimise component count and improve overall panel construction. The ability to interlink multiple pieces and integrate router cut-outs and wiring grooves directly into panels showcased the versatility and ingenuity of AXYZ machines.
The adoption of AXYZ CNC routers by Auto-Trail V.R. Ltd has significantly transformed their manufacturing landscape. By automating key production processes, Auto-Trail has enhanced operational efficiency, reduced costs and maintained high-quality standards in their motorhomes. The successful integration of AXYZ technology showcases Auto-Trail’s commitment to innovation and customer satisfaction, setting a benchmark in the motorhome manufacturing industry.