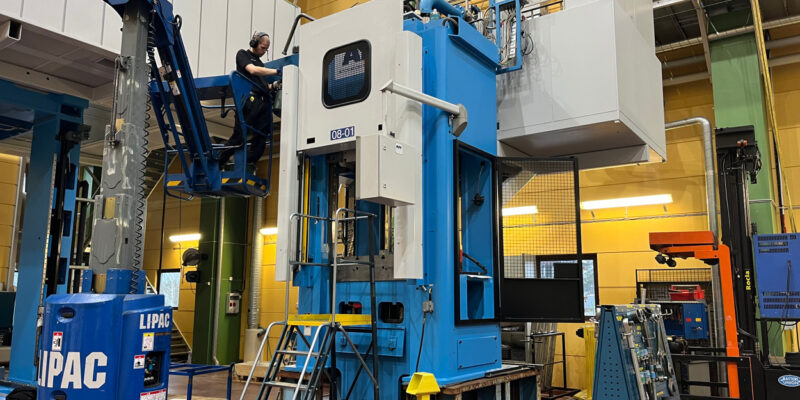
Choosing a refurbished product rather than a newly manufactured one has a significantly lower impact on the climate and environment. And with its attractive pricing, it is also financially beneficial for customers. A customer who recently chose to invest in a factory-refurbished press is Walter Förster in Germany.“At AP&T, we constantly strive to develop our customer offering in a sustainable direction. Part of that strategy is to take care of and renovate older machines and give them a new lease on life,” says Andreas Silfversparre, Manager of Rebuilds & Upgrades at AP&T.
During renovation, the press’s functions are thoroughly reviewed. Parts and systems requiring it are either replaced or upgraded. But the main material of the hydraulic press, steel, is usually kept intact. And since steel production accounts for most of the environmental and climate impact generated by newly manufactured presses, this is where the major sustainability gain comes in.
“We increase circularity and greatly reduce the climate footprint by not scrapping the resource of the press, but rather utilizing it,” says Silfversparre.
Walter Förster chose to refurbish
A customer who recently chose to invest in a factory-refurbished press is Walter Förster in Germany. At the company’s facility outside Hamburg, metal components are manufactured for a range of different purposes, for example medical equipment and parts for the electronics industry. They already have a number of hydraulic presses from AP&T among their production equipment.
“For this type of investment, it is crucial to trust your partner. We have had close and reliable collaboration with AP&T for many years. Their machines are known to be robust, durable and of a very high quality,” says Volker Rohrbeck, General Manager at Walter Förster.
The latest addition was installed and commissioned at Walter Förster in the spring of 2024 – a factory-refurbished hydraulic press, AP&T LPS-2500 with 250 tons of press force, manufactured in the 2000s. With its four cylinder functions, it enables advanced deep drawing operations with several steps in one and the same pressing step. It is a machine that fits Walter Förster’s needs perfectly and increases both flexibility and production capacity.
“When we take in a used press, we always have the customer’s perspective in mind and act proactively where we see that we can meet a specific customer need with a refurbished machine,” says Silfversparre.
Just as in this case. AP&T contacted Walter Förster and presented the idea. The proposal went down well and the order was signed in January 2024. A few months later, the “new” press was in place and in production.
“AP&T’s offer was very beneficial to us, especially for keeping pace with our growth in switchgear production. This press also enabled us to further shorten our delivery times. In today’s fast-paced world, this is a great advantage,” says Rohrbeck.
In addition to the renovation and some customer-specific modifications, AP&T was responsible for transport, rigging, connection of hydraulics, integration with the existing cooling system and commissioning. The deal also includes operator training and an availability agreement, which includes regular maintenance and control of the press’s functions and safety.
“It is not unusual that a press that is properly maintained can have a lifespan of 40 to 50 years and at times, even longer. Right now we are renovating a press from the early 1980s. Once done, we expect it to last for at least another 15 years,” says Silfversparre at AP&T.