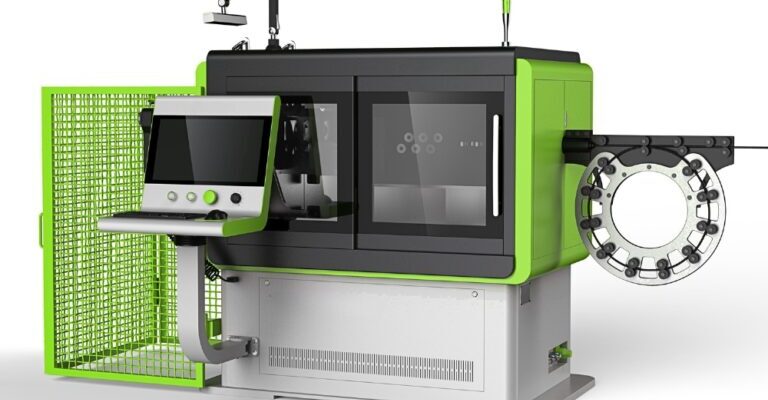
Pneuform, understand the importance of high-quality wire & small bore tube forming machinery in various industries, such as Automotive, HVAC and Construction with a recent surge in EV Bus Bars.
As a leading manufacturer of wire & small bore tube forming machinery, the company prides itself in creating products that are specifically tailored to precise specifications and the unique sector demands.
Pneuform was the first company in the world to produce a complete CNC Tube and Wire two-axis bending machines in the late 70s and then went on to develop the first three-axis machines in the 80s.
These Wire and Tube forming machines are typically used in high volume production and the material is fed from coils, with tube typically being made from copper or aluminium and wire being from pretty much any material and sometimes coated as in the case of EV Bus Bar bending.
The coils of material are then carefully decoiled and straightened through a series of driven rollers to take any inherent twist out of the material.
Once straight the material is then accurately fed through a sleeve into the bending area which is usually a sizeable distance from the main workings of the machine to give maximum clearance.
What is fairly unique to wire and small bore tube forming machines is that the bending head rotates almost 360 degrees around the wire or tube whilst being able to bend in both the clockwise and anti-clockwise direction as well as perform rollforms, making it the most versatile type of bending machine in the market place.
The limitations are usually around the bend quality as the process is akin to compression bending as rollers are typically used for the guiding and bending tools, so tight radius and thin wall tube that are typically need a mandrel are impossible to make on such a machine. Wire of course has none of these constraints which makes it ideal.
The other main difference in the machines when bending tube or wire is around the cutting of the material, typically wire is cut at the bend head end of the machine post bending where are tube is typically spin cut to 80-90% through the wall thickness ahead of the bending process so that it can still be fed into the bending area and snapped off post bending by the operator or the bend head action, the reason for this is reduces the rework on the end of the tube compared to wire where a shear cut is usually acceptable.
Some of the machines can be adapted to include ancillary operations such as End Forming as part of the production process allowing for full automation and robotics.
At Pneuform, we are passionate about pushing the boundaries of wire & tube forming technologies and delivering exceptional products to our valued customers.
Now being part of the Unison Ltd group of companies we now have access to some of their great software and control expertise including Unibend and Opt2Sim ensuring that Pneuform has a long and bright future.