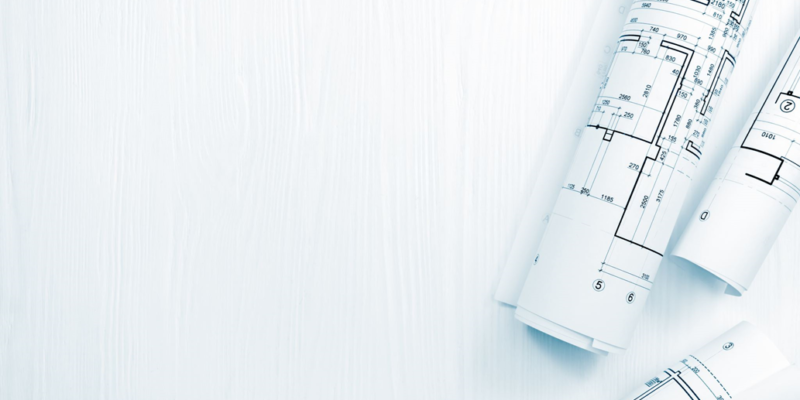
Thanks to Mark Kerwin, Lead Technical Sales Engineer at Fractory
This is an overview of how to optimise sheet metal fabrication for cost reduction in design and production. It covers critical aspects such as material selection, cutting methods, bending techniques, welding, assembly, and prototyping. Following these strategies can help businesses improve efficiency, reduce waste, and enhance competitiveness in sheet metal fabrication.
Sheet metal fabrication is an essential part of manufacturing. At Fractory I work with clients from countless engineering sectors, helping them optimise their sheet metal fabrication requirements, focusing on design and production aspects to reduce costs and improve efficiency.
The Significance of Cost in Design
Cost considerations are paramount in the initial design phase of any product. During this phase, designers face numerous iterations, which can consume valuable time and delay the product’s market entry. Iterations arise from various factors, including consumer feedback, aesthetic improvements and enhanced functionality. But the most significant driver of design iterations is almost always cost. Ensuring competitiveness in the market and winning projects hinges on designing products with cost efficiency in mind. Therefore, it is crucial to weigh the cost implications of your design decisions from the outset.
The Cost Landscape in Sheet Metal Fabrication
Sheet metal fabrication involves several stages, each with its own cost implications. While the exact figures can vary widely from one product to another, as a general guideline, the design phase typically accounts for approximately 5% of the total cost of a product on the market. This cost encompasses expenses related to material, labour and overheads. While it may seem relatively low, the design phase significantly influences the final product’s price. Early decisions can either inflate or reduce costs, making it vital to consider cost-saving measures from the beginning.
Key Cost Factors
To better understand how to improve costs in sheet metal fabrication, it’s helpful to break down the process into five key stages:
- Material Selection: The choice of material is crucial – obviously – in cost management. Research and select materials based on their suitability for your application, considering properties such as yield strength, ductility, and corrosion resistance. Additionally, find out about commonly stocked materials from your manufacturer, as these tend to be more cost-effective due to higher purchase volumes.
- Sheet Size Optimisation: Sheets used in fabrication typically come in standard sizes, such as 3m x 1.5m or 4m x 2m. Maximising material utilisation by ensuring your components have similar thicknesses can lead to cost savings. And consistency in material thickness reduces waste and lowers costs per part.
- Cutting Methods: Choose the most appropriate cutting method based on project requirements. Options include guillotine, punching, flame cutting, oxy cutting, plasma cutting, laser cutting, and water jet cutting. Each method has its cost and quality considerations, so make informed choices based on your specific needs.
- Bending Techniques: Effective bending techniques are crucial for cost reduction. Consider factors such as the minimum flange length required for successful bending and ensure that components are designed with consistency to reduce setup time and costs.
- Welding and Assembly: Explore both manual and robotic welding options, depending on the scale of your production. Robotic welding can significantly reduce man hours and enhance precision, making it ideal for large-scale projects. Additionally, aim to design components that facilitate efficient assembly to decrease labour times. Embrace concepts like poke yoke to simplify assembly without relying on complex jigs.
Material Selection: The Foundation of Cost Efficiency
Material selection is the foundation of cost-efficient sheet metal fabrication. It directly impacts factors such as material waste, production speed, and overall quality. When choosing materials, consider the following strategies:
- Research and Suitability: Thoroughly research materials that are suitable for your application. Ensure they possess the necessary properties, such as strength, ductility, and corrosion resistance, to meet your project’s requirements.
- Range of Materials: Explore a range of materials that could potentially meet your needs. This approach allows for cost comparison during the quotation process, helping you select a cost-effective option.
- Commonly Stocked Materials: Inquire with your manufacturer about the materials they commonly stock or work with. Manufacturers often purchase these materials in larger quantities for various projects, resulting in lower costs per kilogram. Opting for materials readily available to them can save you money.
- Sheet Size Optimisation: When designing components, consider how efficiently they can be nested on standard sheet sizes. Maximising the number of components per sheet reduces waste and material costs. Pay attention to the size of flat patterns and their arrangement on sheets to minimise material usage.
Cutting Methods: Finding the Right Balance
Selecting the appropriate cutting method is essential for cost optimisation. Each method has its advantages and limitations, and your choice should align with your project’s requirements and budget. Here’s a brief overview of common cutting methods:
- Guillotine: Ideal for basic geometric shapes and sheet halving. Typically used for thin-gauge materials but may not provide intricate cuts.
- Punches: Custom tooling punches through the material to cut out features like holes and squares. Suitable for high-volume production but requires initial setup costs.
- Flame and Oxy Cutting: Uses high-temperature flames to cut through metal. Suitable for thicker materials but may leave a rough cut edge, requiring additional finishing.
- Plasma Cutting: Employs a high-velocity ion beam for precise cuts. Suitable for various thicknesses and offers a smoother cut compared to flame and oxy cutting.
- Laser Cutting: Ideal for thin-gauge materials, laser cutting uses computer-controlled mirrors to create precise cuts. It offers high-quality results at a competitive price.
- Water Jet Cutting: Uses a high-pressure water stream with abrasives to cut materials. Provides fine-quality cuts and is suitable for precise detailing but is the most expensive option.
When choosing a cutting method, consider factors such as material thickness, volume, and desired cut quality. While laser cutting is versatile and cost-effective for thin materials, plasma cutting may offer a suitable compromise for thicker gauges. Always test and sample your chosen method to ensure it meets your project’s needs.
Bending: Efficiency Matters
Efficient bending techniques are crucial for cost-effective sheet metal fabrication. Consider the following strategies:
- Standard Tooling: Choose tooling that aligns with commonly used flange lengths and radii. This reduces setup time and costs, as operators can work with consistent tooling for multiple components.
- Bending Guidelines: Familiarise yourself with bending guidelines, including the minimum flange length (B dimension) required to secure the material in place during bending. Avoid placing holes or features within this critical bending area to prevent deformations.
- Consistency in Design: Design components with consistent bend radii and flange lengths to streamline production. Consistency reduces setup time and allows for faster, more efficient bending.
For more information on bending, take a look at the Fractory bending calculator.
Welding and Assembly: Finding the Right Approach
Effective welding and assembly processes are essential for cost optimisation in sheet metal fabrication. Consider the following strategies:
- Welding Methods: Choose the appropriate welding method for your project. Manual welding is suitable for smaller volumes and intricate components, while robotic welding excels in high-volume, repetitive tasks.
- Robotic Welding: If applicable, invest in robotic welding for large-scale production. While the initial investment can be high, the long-term cost savings in labour and consistency are often substantial.
- Design for Assembly: Design components that are easy to assemble, minimising the number of fasteners and complex assembly steps. Reducing assembly complexity leads to lower labour costs and shorter production times.
- Assembly Jigs: Consider the use of assembly jigs or fixtures for consistent and efficient assembly. While they may require initial investment, jigs can save time and ensure precise assembly.
- Poke Yoke Design: Implement “poke yoke” or error-proof design principles to minimise errors during assembly. By ensuring components can only be assembled in one orientation, you reduce assembly time and the likelihood of costly mistakes.
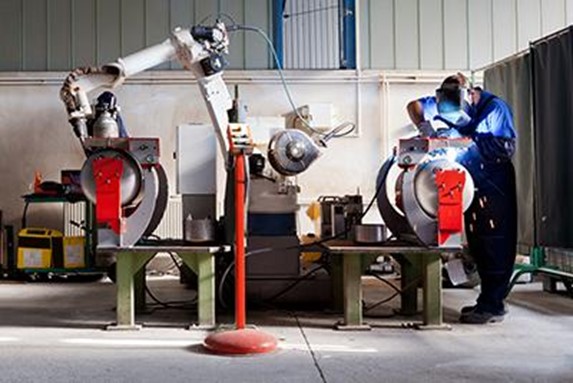
Prototyping and Testing: Reducing Costly Revisions
Prototyping and testing are crucial phases in the design process, but they can also be costly if not managed efficiently. To reduce expensive revisions and iterations, follow these guidelines:
- Virtual Prototyping: Leverage virtual prototyping tools to simulate your sheet metal components and assemblies. This allows you to identify and rectify design issues before physical prototypes are created, saving time and money.
- Rapid Prototyping: When physical prototypes are necessary, explore rapid prototyping methods like 3D printing. These technologies can quickly produce prototypes for evaluation at a fraction of the cost of traditional methods.
- Testing and Validation: Conduct thorough testing and validation of prototypes to ensure they meet design specifications. Address any issues promptly to avoid costly rework during production.
Conclusion: The Path to Cost-Effective Sheet Metal Fabrication
Sheet metal fabrication is a critical part of manufacturing, and optimising costs in its design and production will improve competitiveness and profitability. By implementing cost-effective strategies from the outset, you can lower expenses, reduce waste, and improve efficiency. Remember to consider material selection, cutting methods, bending techniques, welding, assembly, and prototyping to find the right balance for your specific project needs.