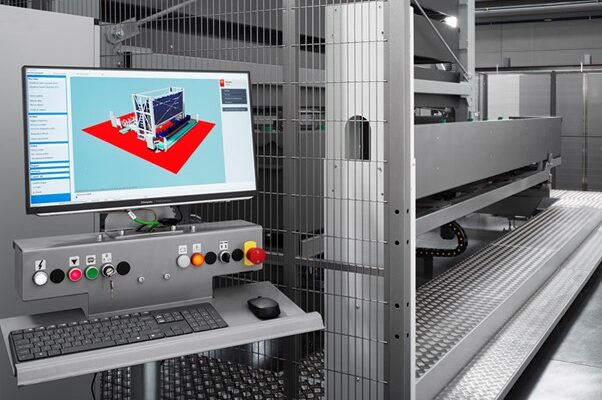
The subject of material loading and unloading automation is well established in sheet laser cutting with a multitude of solutions and complexity. In contrast, BLM’s tube laser cutting systems equipped with vertical storage systems, for tubes and section bars, capable of handling bars automatically and allowing for unmanned production changes have only been available for a few years.
1. Increase daily productivity
An automatic tube tower storage system is a steel structure in which a number of crates are loaded, each containing tubes made of steel, copper, iron, aluminium or any other metal of various cross-sections and thicknesses.
Depending on the batch to be processed, the tube to be cut is automatically and quickly taken from its crate to the machine loader, so that laser cutting of the tube can begin without waiting and without the need to involve additional operators, such as forklift drivers, storage system managers, etc.
The result is a system that can start producing faster, much faster than if the tubes need to be handled manually.
If you also consider the time required to remove the bars from the loader from the previous batch and the time required to put them back in place, you can immediately see why the uptime of the laser tube cutting system is decisively increased, the waiting downtime of the machine is reduced, and daily productivity is boosted as a consequence.
2. Change job priorities immediately
Sometimes you may need to change the order of the planned batches (in some cases, even by discontinuing the current batch) to deal with emergencies and unexpected changes in production needs. An automatic material change solution makes this a minor inconvenience.
There is no need to find space to temporarily lay tubes and section bars aside which means no handling complications and no risk of losing track of pending work.
The order of the queued batches can be changed directly on the machine or an additional batch is added to the pre-programmed list, with an automatic crate change achieved in a short time.
Production changeovers are immediate using the tower storage system.
3. Gain space in the workshop
We have already mentioned the need to extract the material leftover from a previous batch to free up the machine storage system and start a new batch.
The material must be removed so it is not in the way and does not obstruct the arrival of the new tube bundle. If the bars needed for a series of batches already planned are to be prepared in advance, the management of the space around the machine becomes even more delicate, because a large part of it will have to be used for activities that do not create added value, but simply as a temporary parking point for bars waiting to be processed.
This situation can be improved by an automatic vertical tower storage system that allows the height of the workshop to be exploited and frees up the area around the machine, which can then be used for more profitable purposes.
4. Managing material stocks in real-time
By interfacing the storage system with the company’s management system (in addition to the advantages of machine integration), material stocks are monitored for better and more flexible management of production plans.
At the end of batch processing, the tubes that are not taken out of the loader and thus not used, are returned to the crate and properly recounted, and the crate is placed back in its rack inside the tower.
By knowing precisely how much material is available in the various crates, it is possible to optimize the periodic filling of the tube storage system, evaluate different material management strategies and manage plans from the office.
5. Protecting the material
Manually moving heavy and cumbersome bundles of tubes back and forth from the central storage system to the machine, while many other activities take place around it, is not only a cause of inconvenience and a potential source of risk for operators but can also affect the surface quality of the tube.
Caution and care in handling the bars may not be sufficient to avoid knocks and misshaping, even if only due to the way the tubes are lifted or supported.
The defects that accumulate on the tubes cause both production and material waste. Even more critical are the cases in which the available quantities are limited.
An automatic tower storage system for tubes helps to preserve the surface quality of the tube to be processed by keeping it in a more protected space and optimizing handling to minimize any imperfections.
6. Ensuring greater safety for the operator
The reasoning is similar but even more important with regard to manual and potentially dangerous activities for operators and other people around the systems.
With fully-automated loading and unloading, the storage system can be filled at a precise time of the day, under the best “internal traffic” conditions, taking advantage of improved raw material logistics.
There is no longer the continuous and fragmented involvement of means and resources, but a single phase of preparation for the planned sequence of batches.
7. Ensuring continuity and reliability in automated unmanned processing
The production of small batches at large-scale costs becomes possible through shorter machine set-up times between batches.
An automated tower storage system enables unmanned processing, resulting in lower costs and higher productivity.
By eliminating any possibility of error and achieving independence from the operator experience, an additional margin of efficiency and reliability of time and cost estimates is achieved.
Conclusions
Today, maintaining competitiveness is an ever-greater necessity, solutions are constantly being sought to increase the efficiency of individual processes, simplify internal logistics in material handling and stock management, and contain the high costs of hard-to-find specialized labour, while still maintaining high standards of safety and protection.
The use of a tower storage system in tube and bar processing is a solution that goes in this direction, even more so when combined with other services, such as the generation and in-depth analysis of production data from the machines, to the monitoring of material and personnel flows and to production systems capable of interconnecting and exchanging data to increase production flexibility.
An automated storage system for tubes and section bars means that competitiveness is no longer just the result of lower resource and personnel costs, but above all making the most of renewed industry 4.0 technological potential.