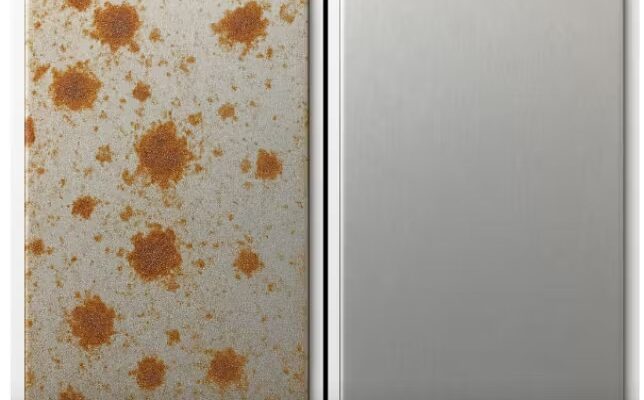
If you’ve ever found yourself wondering whether to go with 304 or 316 stainless steel, you’re not alone-and you’re asking the right question. While these two stainless steel grades may look nearly identical to the untrained eye, what’s hiding beneath the surface could make or break your next project.
So, what really sets them apart? Is it the price? The resistance to rust? Their performance in demanding environments?
This article cuts through the confusion and delivers a clear, side-by-side comparison of 304 vs. 316 stainless steel, covering their composition, properties, real-world applications, and, of course, the all-important cost considerations.
Whether you’re a product designer, engineer, procurement lead, or just stainless steel-curious, this guide will help you make the smartest material decision for your needs.
Composition and Chemical Properties
At first glance, 304 and 316 stainless steels may seem interchangeable; they are both part of the austenitic stainless steel grades, share a similar appearance, and even have overlapping uses of stainless steel.
But the real distinction lies beneath the surface, in their chemical makeup.
The basics: What’s in the mix?
Both 304 and 316 stainless steels are iron-based alloys enhanced with chromium and nickel to give them their signature corrosion resistance and mechanical strength. However, the difference comes down to one critical element: molybdenum.
- 304 stainless steel contains chromium (18–20%) and nickel (8–10.5%), which gives it excellent general corrosion resistance.
- 316 stainless steel builds on that foundation with the addition of 2–3% molybdenum, significantly improving its resistance to chlorides, saltwater, and industrial chemicals.
That small percentage of molybdenum makes a big impact-and often determines which grade is suitable for more aggressive environments.

If your project is likely to encounter harsh chemicals, seawater, or salt spray, the molybdenum in 316 is your best friend. For more general indoor or mild outdoor applications, 304 is typically more than sufficient.
Mechanical Properties
While composition reveals what each grade is made of, mechanical properties tell us how they perform under stress-which is critical when choosing materials for manufacturing, construction, or high-load applications.
Both 304 and 316 stainless steels are known for their excellent mechanical performance, especially when compared to mild steel or ferritic stainless grades. However, subtle differences can guide engineers and designers toward the most efficient and durable choice for their projects.
Key mechanical properties compared
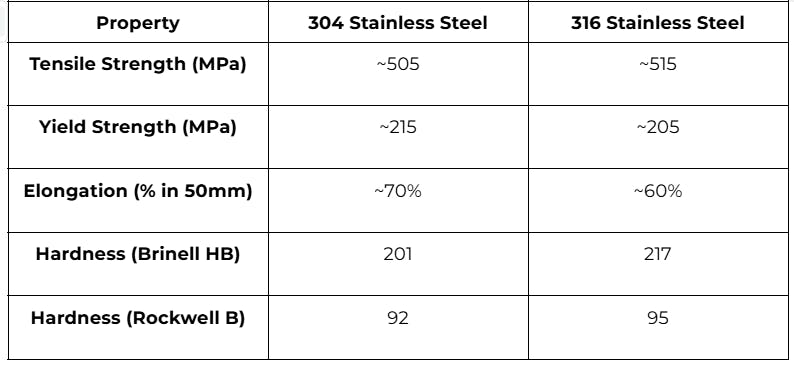
What does this mean for your project?
- Tensile and yield strength: Both grades offer solid performance, but 316 has a slight edge in ultimate tensile strength, making it more durable under sustained loading. That said, 304’s slightly higher yield strength means it resists deformation just a bit better at lower stress levels.
- Hardness: 316 is marginally harder, which can improve wear resistance in abrasive environments-but the difference is small and often not a deal-breaker.
- Ductility (Elongation): 304 has the upper hand in ductility, meaning it can stretch more before breaking. This makes it a solid choice for deep drawing, stamping, or forming operations, where flexibility matters.
Application-driven choices
- For components requiring deep forming or bending, 304 is often preferred due to its superior ductility.
- For mechanical parts exposed to heavy loads and wear, 316’s added tensile strength and hardness may offer longer life and better performance.
- In abrasive or slightly corrosive industrial environments, 316 can outperform 304 by maintaining its mechanical integrity even as it resists corrosion.
Corrosion Resistance
If there’s one area where 316 stainless steel truly shines, it’s here.
While both 304 and 316 stainless steels are highly resistant to rust and corrosion, the presence of molybdenum in 316 significantly boosts its performance in aggressive environments-especially those involving chlorides (like saltwater) and harsh chemicals.
A side-by-side comparison of 304 and 316 stainless steel in a salt-spray test:
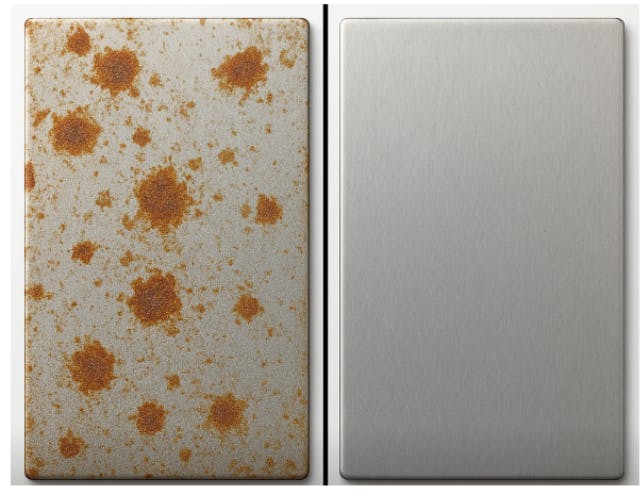
Quick decision tip
If your application never sees salt, chemicals, or harsh weather, 304 is a cost-effective and reliable option. If you’re dealing with marine, coastal, or industrial environments, don’t compromise-go with 316.
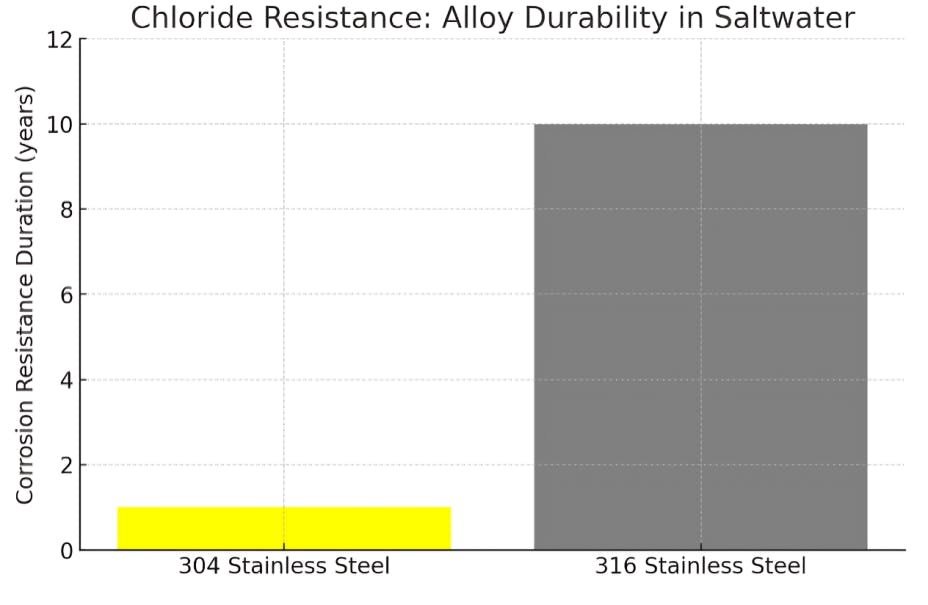
The chart compares the corrosion resistance of 304 and 316 stainless steel in a simulated saltwater environment, showing that 316 lasts significantly longer, with a resistance duration of 10 years compared to 304’s 1 year.
Common Applications
Understanding where and why 304 or 316 stainless steel is used can help make the decision far easier. Each grade excels in different settings-not just based on cost, but also based on environmental exposure, hygiene standards, and structural requirements.
Let’s look at where each stainless steel grade is commonly used in the real world.
Applications of 304 stainless steel
Often referred to as the “workhorse” of stainless steel, 304 is used across countless industries thanks to its balance of strength, corrosion resistance, and affordability.
Common uses of stainless steel, like 304, include:
- Kitchen equipment: sinks, countertops, splashbacks, cutlery
- Food and beverage production: brewing vessels, milk tanks, storage silos
- Architectural and structural components: railings, balustrades, decorative panels
- Household hardware: doorknobs, brackets, bolts, and fasteners
- Automotive trim: especially in dry environments
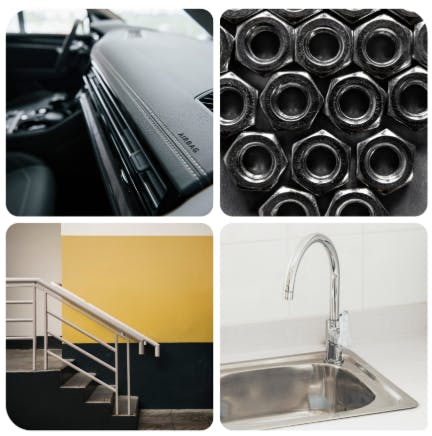
For sheet metal fabrication, 304 stainless steel is a reliable choice due to its ease of welding and forming, making it a popular option for various applications.
Why 304? It’s versatile, easy to fabricate, and offers solid corrosion resistance in typical indoor or low-exposure conditions.
Applications of 316 stainless steel
When performance under pressure (or in salt!) is non-negotiable, 316 stainless steel steps up. Thanks to its enhanced resistance to corrosion-especially from chlorides-it’s the top choice in marine, medical, and chemical environments.
Common uses of stainless steel, like 316, include:
- Marine components: boat fittings, dock hardware, propeller shafts
- Medical devices: surgical instruments, orthopedic implants
- Chemical processing equipment: tanks, valves, pipelines
- Pharmaceutical and food processing: cleanrooms, sanitary piping
- Outdoor structures: exposed fasteners, sculptures, enclosures in coastal or industrial zones
If you’re looking to work with CNC machining materials that require higher corrosion resistance, 316 stainless steel is often the superior choice for industries exposed to harsh chemicals or saltwater.

Application Comparison Table
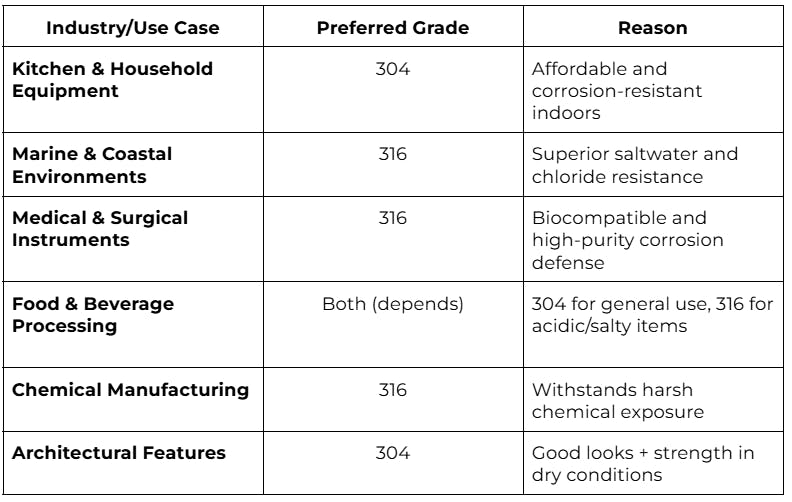
Cost vs. Performance: When to choose which

Making The Right Choice Between 304 and 316 Stainless Steel
When it comes down to it, both 304 and 316 stainless steels are exceptional materials-each with their own strengths.
- If your project is indoors, in a low-corrosion environment, or you’re working with a tight budget, 304 is a smart, versatile, and cost-effective choice.
- If you’re dealing with saltwater, chemicals, or high-value components where failure is not an option, 316 offers that extra layer of protection and peace of mind.
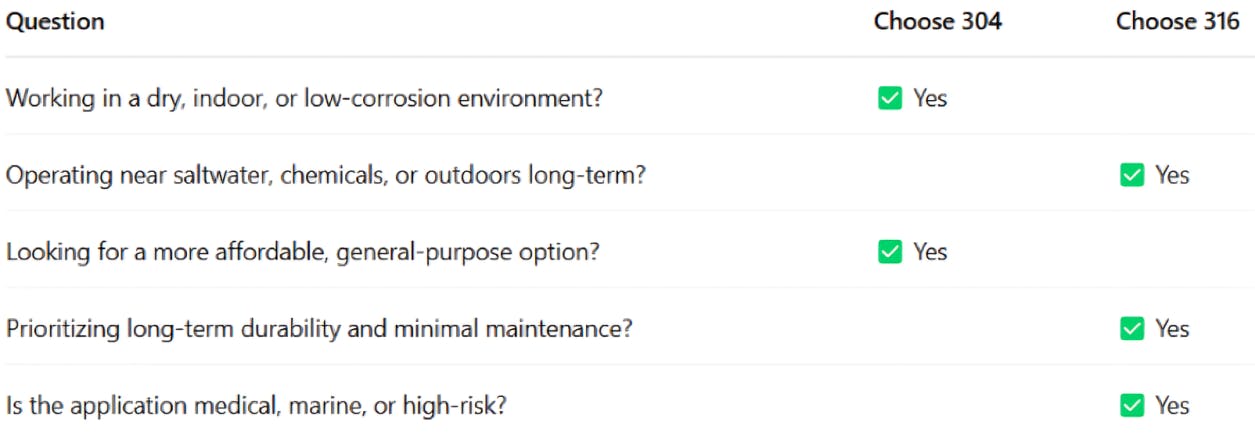
Your choice should always be guided by the environment, the application, the lifecycle cost, and of course, how critical performance is to your bottom line.