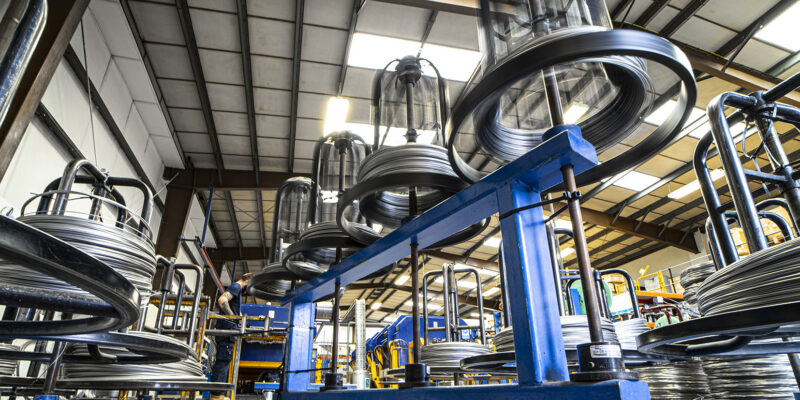
Over £200,000 of new equipment has been installed at Alloy Wire International (AWI) and is set to deliver more than £2m of additional capacity.
The manufacturer of round, flat and profile wire has got its two single hole blocks, 3-hole dry drawing machine and 4-spindle spooler now fully operational at its state-of-the-art factory in the West Midlands.
This will give the business the ability to reduce lead times even further, whilst also allowing it to offer clients in the automotive, aerospace, defence, oil and gas and medical sectors with access to larger volume quantities.
Bosses have also pressed the button on upgrading its tensile testing machinery, which will help it speed up the pre-job trial process and broaden the range of support offered to customers throughout the full duration of projects.
“We had our best April on record for outgoing orders and the pipeline of activity shows no sign of things slowing down,” commented Andrew Du Plessis, Technical Director of Alloy Wire International.
“The decision was made last year to embark on a £500,000 investment drive and these latest installations are an important part of this strategy. Each one has been tailored to suit our specific production requirements and to have them operating on the shop floor is great to see.”
He continued: “Our success is all about making sure we are ahead of the competition when it comes to manufacturing agility, quality and delivery performance. The latter already sees us produce wire in three weeks, nobody else can do that.
“This investment reinforces this capability, as well as giving us nearly £2m of additional capacity to work with.”
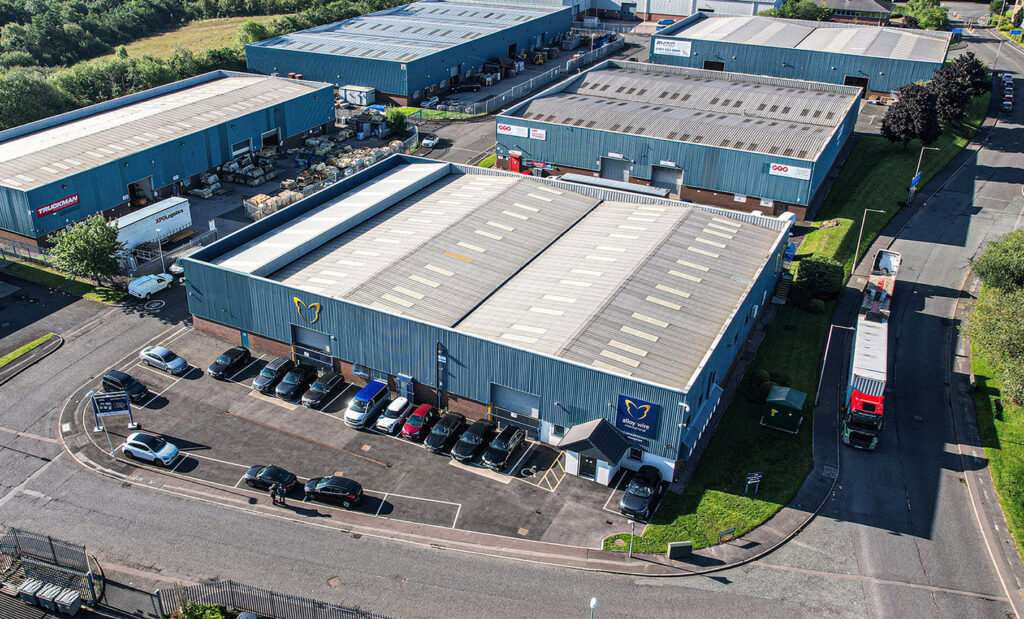
Alloy Wire International is passionate of the ‘Made in the UK’ brand, exporting its 60-strong range of exotic alloys to 65 countries.
This means material made and tested in its factories in Brierley Hill and Yorkshire is used as far away as Azerbaijan, Australia, Kuwait, Kazakhstan and India.
Export success has not been a new thing for the company, in fact it has been trading internationally for 77 years, building a strong sales agent network with representatives on the ground in its core European, Chinese, Australian and US markets.
This has really paid off in the latter, delivering its largest ever export order (worth $400,000) to supply a high strength nickel cobalt alloy to a US springmaker.
Andrew went on to add: “The investment doesn’t stop there, with a new £90,000 linisher due for August this year, closely followed by a dry drawing pointer.
“All of this will ensure AWI continues to be known for our mantra… ‘manufacturing quality – delivering reliability, a mantra that sees us hold the AS910 (Aerospace), ISO:9001 (Quality), ISO:13485 (Medical), ISO:14001 (Environmental) and ISO:45001 (Health & Safety) quality accreditations.”