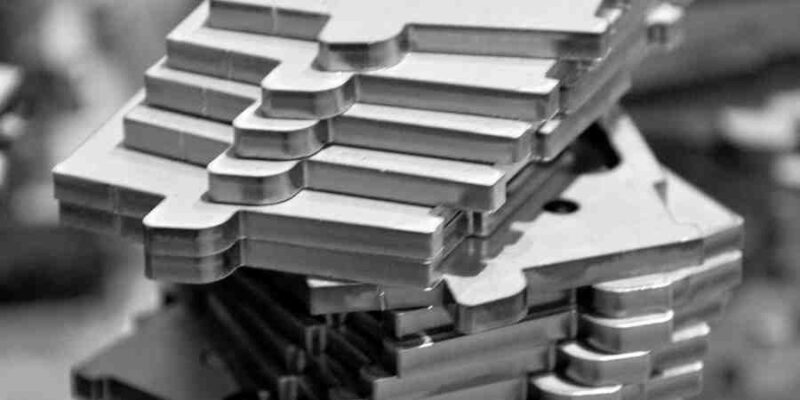
In the heart of the UK’s bustling manufacturing and design sectors, this relatively new engineering technology stands out as a beacon of innovation and precision. This advanced technique, pivotal in shaping materials into intricate designs and components, has become indispensable across various industries, including aerospace, automotive, construction and fashion. This post delves into the technical nuances of cutting, its applications, and its significance within the UK’s dynamic manufacturing landscape.
Understanding Laser Cutting / Profiling
At its core, this engineering process is a non-contact, thermal-based process that uses a focused laser beam to melt, burn, vaporize, or blow away material, leaving a high-quality finish. The process can be divided into three main types: fusion cutting, flame cutting, and remote cutting, each suitable for different materials and applications. Fusion cutting uses a laser to melt the material in a controlled manner, assisted by a gas that ejects the molten material and creates a clean cut. Flame cutting, on the other hand, relies on a laser beam to heat the material to ignition temperature, with an oxygen jet to drive the combustion process and expedite the cutting. Remote cutting, a newer technique, leverages the high power of the laser to cut thin materials without the need for a gas jet.
Technical Specifications
The technical prowess of laser profiling machines is measured in several key specifications: laser power, cut speed, precision, and material compatibility. Laser power, typically ranging from a few hundred watts to several kilowatts, dictates the thickness and type of materials that can be cut. The cut speed, precision, and material compatibility, on the other hand, depend on the type of laser (CO2, Nd:YAG, or fiber laser) and the machine’s design and settings. CO2 lasers are versatile and suitable for cutting, engraving, and marking a wide range of materials. Nd:YAG lasers, offering higher peak power, are ideal for metals and hard materials. Fiber lasers, known for their efficiency and cutting speed, are increasingly popular for metal processing. The UK market is dominated by a small number of global players including Trumpf, Bystronic and Amada.
Applications in the UK
In the UK, the adoption of cutting technology spans across sectors, driven by its versatility and the demand for precision manufacturing. In aerospace, laser cutting is used to produce lightweight, high-strength components critical for aircraft performance. The automotive industry utilises laser cutting for producing complex components with tight tolerances, contributing to vehicle efficiency and safety. Furthermore, the creative industries, including fashion and architecture, leverage laser cutting for designing intricate patterns and structures, pushing the boundaries of traditional manufacturing.
Challenges and Innovations
Despite its advantages, laser cutting faces challenges such as thermal distortion, material limitations, and the need for constant innovation to stay ahead in a competitive market. Addressing these challenges, UK manufacturers and researchers are pioneering advancements in laser technology, such as the integration of artificial intelligence for optimized cutting paths, and the development of new laser sources that offer greater efficiency and material versatility.
Conclusion
This cutting technology represents a fusion of precision, versatility, and innovation, playing a crucial role in the UK’s manufacturing prowess. As the industry continues to evolve, the ongoing advancements in laser cutting will undoubtedly propel the UK further onto the global manufacturing stage, cementing its position as a leader in high-tech, precision engineering. In embracing these technological strides, the UK is not just cutting materials; it’s shaping the future.