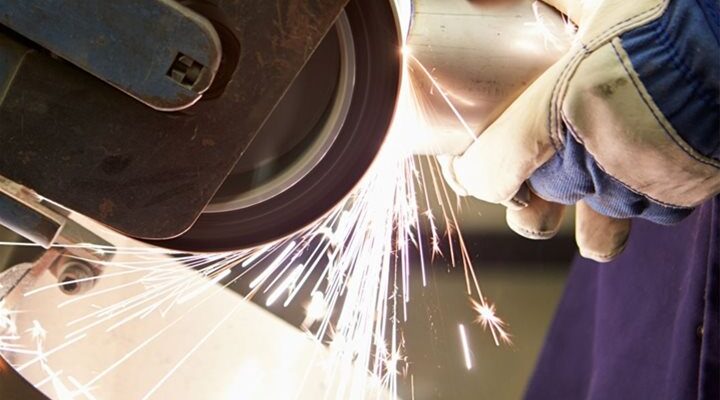
You may have heard the term finishing before, but linishing is a more uncommon, specialist term within the metalworking industry. Linishing is the process of either manually or by using a machine typically, a linisher or belt sander, to grain or polish the surface of sheet metal or a component.
Linishing equipment comes in different sizes and configurations, ranging from handheld abrasive strips and blocks for detailed work to larger y static machines for more industrial applications. The choice of abrasive grit and compound used depends on the desired finish and the characteristics of the metal being processed.
What is the difference between finishing and linishing?
Actually, linishing is a type of finishing. While finishing is a broad term that can involve grinding, polishing, buffing or coating a metal workpiece, linishing is a specific type of finishing that uses abrasive belts or wheels to remove material from the surface of a workpiece, producing a consistent grained finish ranging from course to ultra-fine.
The term finishing is broad enough to apply to various industries, such as woodworking. However, linishing is a much more specific term that applies predominantly to the metalworking industry.
How does linishing work?
Linishing involves using a machine, often referred to as a linisher or belt grinder, to finish and refine the surface of a metal workpiece. Here’s how linishing typically works:
- Choose Abrasive Materials: A linishing machine is equipped with belts or wheels made of materials like sandpaper, emery cloth or other abrasive compounds. Depending on the desired finish, the type of metal being processed, and the level of material removal required, different abrasive materials and grit sizes may be used.
- Secure the Workpiece: The metal workpiece is held down or clamped in place on the linisher, ensuring stability during the linishing process. Correct placement helps prevent vibrations and movement, allowing for precise and controlled material removal.
- Adjust Settings: The machine operator adjusts various settings on the machine, like belt tension, speed, and pressure, to achieve the desired results. Different materials may require specific settings to optimise the process.
- Begin the Abrasive Action: When the linisher is activated, the abrasive belts or wheels begin to rotate. The operator or the machine conveyor guides the workpiece against the abrasive. Material Removal: As the abrasive surface comes into contact with the metal workpiece, it removes a controlled amount of material from the surface. This helps to smooth out irregularities, eliminate burrs, and refine the texture of the metal.
- Achieving Desired Finish: The process continues until the desired level of surface finish is achieved. The operator might change the belts or wheels to refine the surface to attain the desired finish.
- Final Inspection: After the linishing process is complete, the workpiece is inspected to ensure that the surface finish meets the specified requirements.
If necessary, additional operations like polishing or buffing may be performed to achieve the desired appearance.
Key Points About Linishing
If you’re looking for more information about linishing, here are a handful of key points to take away with you.
Linishing Removes Material
Linishing is an abrasive machining process that removes material from the workpiece’s surface to achieve the desired finish.
Linishing Provides a Consistent Finish
The linishing process helps create a uniform and consistent surface texture across an entire workpiece.
Versatility of Linishing
Linishing is often used for deburring and removing sharp edges, as well as generating a surface finish. In addition, linishing machines are versatile and can be used on various metals including mild steel, aluminium, and stainless steel with the correct choice of abrasive compound.
Linishing Is a Metalworking Process
Linishing is commonly used in metal fabrication, sheet metal manufacturing, and other industries where achieving a smooth and refined surface finish is important. The process allows for precise control over the level of abrasion, enabling operators to achieve specific surface finish requirements.